The new Hazira Container Terminal at Adani Port, in Gujarat, India, reports that since its opening day in January 2013, it has achieved approximately 50 percent greater cargo-management efficiency than other terminals of the same size, by deploying a radio frequency identification system. With the terminal-operations solution, provided by Suraj Informatics Pvt. Ltd. (SIPL), the terminal indicates a turnaround time of less than 30 minutes for trucks arriving to load or unload cargo—about half the time required for such operations at similar terminals.
A steady stream of truck traffic passes through Adani Port, situated on the west side of the Hazira peninsula, to move cargo to and from Europe, Africa, the Americas and the Middle East. Goods enter and exit the port via ocean vessels. Because the terminal lacks rail facility, however, trucks provide the only means of moving cargo onto and off of ships. In addition, the terminal has only a 600-meter (1,970-foot) wharf to accommodate all of the vehicles.
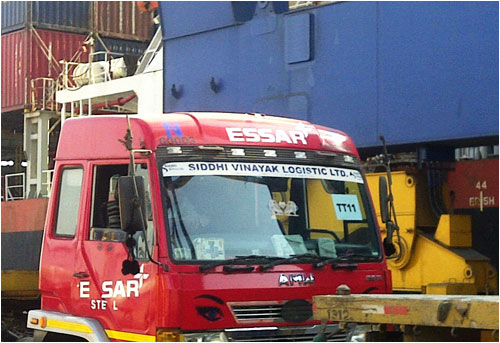
As a result, traffic management is challenging for the terminal, and managers strive to prevent backups in which truck operators wait to load or unload goods. In mid-2012, Hazira began seeking a solution that would automate the processes of tracking vehicles at the gate, as well as while they are loaded or unloaded, and thereby make operations more efficient, prevent mistakes (for example, the loading or unloading of cargo at the wrong location) and require less waiting time for shipping customers.
Adani Port chose to install an RFID system that would provide data regarding truck movements. The solution is integrated with the terminal’s existing Terminal Operating System (TOS), enabling the port to automate the gate-entry process for vehicles and provide better location data in the shipping yard, as well as at the wharf. It would also reduce the need for personnel to check truck ID numbers at loading and unloading areas, in order to ensure that a vehicle is at the proper location, and to create a record of its processes at the terminal.
The port began working with SIPL to develop a passive ultrahigh-frequency (UHF) RFID solution in August 2012, according to Rajeshwar Bhatt, SIPL’s director. It tested tags on trucks read by interrogators located at the gate, Bhatt says, and fully installed the solution in January of this year. By deploying readers at the entrance and exit gates, and by supplying trucks with tags, the port can utilize SIPL software hosted on its back-end system to determine which trucks have arrived for which particular container. Additional readers installed on loading equipment identify vehicles and ensure that there are no errors, such as unloading cargo at the wrong location, or loading the incorrect goods onto a vehicle.
Upon arriving at the port gate, a driver receives a temporary passive UHF RFID tag (an M-Crown ruggedized tag from The Tag Factory, with a built-in Impinj Monza 4 chip), which can be attached to the center of the dashboard inside the vehicle’s cab via an adhesive. Staff members at the gate enter the tag’s ID number, along with data about the vehicle and the load it is receiving or delivering. The unique ID encoded to the tag is then linked in the SIPL software to information regarding the trucking company, the vehicle and the goods being transported. The SIPL software then forwards that data to the terminal’s TOS solution, and the TOS software prints a receipt for the driver.
The truck then proceeds past a pole-mounted RFID reader (the SIPL system includes interrogators from both Motorola and FEIG Electronic), which captures the tag’s ID number and forwards it to the TOS software. This updates that vehicle’s status as having arrived at the terminal, and prompts the gate to open, allowing that truck to enter.
Next, the driver navigates the vehicle to the wharf location indicated by the gate staff, where goods are either loaded or unloaded using a rubber-tiered gantry (RTG) or a quay crane (QC). The vehicle’s tag is then read again by a reader installed on the RTG or quay crane. That data is sent to the back-end database via a Wi-FI or GPRS connection, after which the TOS software displays information about the vehicle for the RTG or QC operator on his or her onboard computer. The operator can then discharge or load the container as required for the assigned job, and that data is stored in the Terminal Operating System.
After the loading or unloading process’ completion, the truck proceeds to the exit gate, where the tag is again read by another interrogator. The TOS solution prints an exit-gate pass, and the terminal’s boom barrier opens, allowing the truck to pass out of the terminal toward the port gate.
At the port gate exit, a tag dispatcher is assigned to retrieve the truck’s tag. A reader installed at the gate interrogates the tag a final time as it is turned over to the staff, and the TOS software prompts the port gate boom barrier to open, enabling the truck to leave the port.
Altogether, the terminal has installed two readers each at the port entrance and exit, as well as two at each entrance and exit to the terminal itself. In addition, each RTG and QC comes equipped with a reader and an antenna, totaling approximately 70 readers. At gates and on the RTG, Bhatt says, the tag can be read from a height of up to about 3 meters (9.8 feet), while the read range on the QC can reach 8 meters (26.2 feet).
By using the technology, the port has decreased truck waiting times and labor costs, Bhatt reports. “Since there is no data entry at the gate and yard,” he states, “the process has reduced the transaction time at the gate for each truck, along with data-entry time of the RTG operator for selection and updating each job.” What’s more, he adds, terminal management now knows the exact number of trucks present in the yard at any given time. The TOS solution can also issue alerts in the event that a vehicle takes more than the expected transaction time.
The system is anticipated to save the terminal about $112,000 (6.7 million lahks) annually in labor costs. During a future phase of the SIPL system at the terminal, additional RFID readers will be installed throughout the yard, in order to provide container-location mapping that will help terminal managers view each vehicle’s exact position within the yard in real time, as well as collect historical data for use in traffic-flow management.