A recent article in The New York Times points out that 70,000 bridges in the United States are structurally deficient. It is imperative that structural anomalies on aging infrastructure be detected and corrected in a timely manner, to avoid disasters such as the 2007 St. Anthony Falls Bridge collapse in Minnesota.
To maximize the chance of detecting the onset of surface cracks in concrete and other construction materials, sensors must be deployed pervasively. Structural engineers have focused primarily on wired strain gauges and accelerometers to detect structural faults. These sensors work well, but the management of lead wiring can be prohibitive. Wireless counterparts exist, but they are cost-intensive and so do not lend themselves to pervasive deployment.
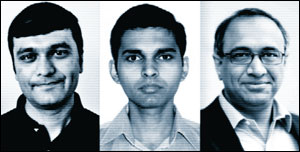
At the Auto-ID Lab at the Massachusetts Institute of Technology, we are developing a solution using ultrahigh-frequency RFID tags. The tag’s antenna serves as a sensor capable of detecting a surface crack. The development of a crack severs the tag’s antenna, manifesting in a drop in strength of the signal with which the tag responds to a reader. The tag’s unique ID is associated with the crack’s location. We believe this is an ideal approach, because RFID tags can be manufactured in mass quantities for very low cost, and they have a proven track record for large-scale object tracking in many industries.
The crack-detector tag is deployed on the concrete surface in two stages. First, the tag’s antenna, which is made of conductive copper ink, is painted onto the concrete surface. The copper ink forms a strong bond with the concrete. Next, the tag’s integrated circuit is connected electrically to the antenna.
We can create a crack-detection grid using an array of such RFID tag sensors on a concrete surface. When a crack propagates, it cuts the antennas of some of the tags in the grid. By observing which tags register a drop in signal strength, it is possible to identify the length and direction of the crack’s propagation to determine where structural repairs are needed.
While the design idea is feasible, it is still in the development stage. We are considering several deployment challenges before this technology is ready to be field-tested. We are investigating the use of polyester coatings to protect the grid, which is attached to the concrete, from moisture, acid and animal attack. We are also trying to extend the read range of the sensor grid to 13 to 20 feet, so we can monitor the tags using RFID readers deployed on vehicles passing near or under the concrete surface. Other challenges include improving the grid’s spatial resolution and sensitivity to cracks of different widths.
Rahul Bhattacharyya is associate director of the Auto-ID Lab at the Massachusetts Institute of Technology. Prasanna Kalansuriya is a visiting researcher at the Auto-ID Lab. Sanjay Sarma is a professor of mechanical engineering at MIT and a co-founder of the Auto-ID Lab.