An ambitious pilot in the Netherlands, known as “van Plant tot Klant” (From Plant to Customer), is testing how well RFID technology can be used to reduce labor and increase the efficiency and accuracy of the shipment of potted plants throughout Europe. The Florilog Foundation (which aims to improve the horticultural supply chain by developing projects focused on gaining efficiency), located in Honselersdijk, is funding the project on behalf of Productschap Tuinbouw, a Dutch association consisting of members of the horticulture industry. The system, provided by Interaxi, includes EPC Gen 2 passive ultrahigh-frequency (UHF) RFID tags to track trays of plants from two growers in the Netherlands, through the hands of logistics providers and exporters, to transport companies’ distribution centers, before the trays are then shipped to retailers.
The Dutch plant industry is seeking an automated system that would save space and time for members of the products’ supply chain, while also reducing errors. RFID, the project’s participants believe, offers an option by which tags on plant trays and trolleys could be read without manual intervention, thereby saving workers time that would otherwise be spent confirming orders and manually writing down order numbers of arriving and departing shipments.
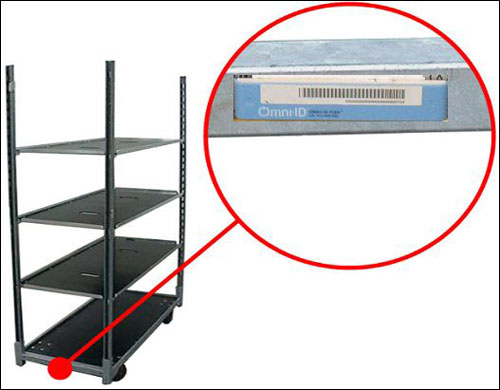
The project, which began in the first quarter of 2009, includes two growers: Oriental Group, which grows bonsai, bamboo and other plants found in Asia, and Zuydgeest de Lier, which grows Calandiva (a Kalanchoe cultivar) and other flowering plants, all of which are purchased by buyers throughout Europe. Zuydgeest and Oriental Group ship plants from their greenhouses to a DC operated by logistics-management firm Sierteelt Direct, in the neighboring city of Naaldwijk. At Sierteelt’s DC, the plants are sorted according to orders, and are then transported to exporters such as Hamiplant (each exporter ships product to different parts of Europe, such as France or Germany). The exporters’ employees then rebuild the trolleys according to specific orders, and transport companies, such as Breewel Transport (which is also participating in the RFID pilot), pick up the plants via truck and transport them to retailers throughout Europe. In some cases, such as with shipments sent to Paris, the product is further broken down into smaller shipments at a DC, and then loaded onto smaller trucks for delivery to specific city neighborhoods.
Often with little understanding of what is happening with supply chain partners, logistics firms, exporters or transport companies can be taken by surprise when multiple orders arrive unexpectedly, or fail to arrive when expected. The plants must move quickly through the supply chain, and a lack of information communicated between supply chain partners can cause delays, as well as excessive labor costs to keep up with the unpredictable need throughout the day for manpower to process the plants as they arrive or need to be shipped.
For the Plant to Customer project, participants employed RFID to help them track the locations of shipped plants, and to share information regarding the receipt and subsequent release of each tray of potted plants to the next recipient, on a server hosted by Interaxi. For plants being shipped to those pilot participants, the two growers applied passive UPM Raflatac EPC Gen 2 RFID tags to plastic trays on which plants are placed Those trays are then put onto wheeled metal trolleys, explains Erik Heemskerk, Interaxi’s new business developer. The trolleys themselves also have an Omni-ID Flex EPC Gen 2 tag attached to the center front of the bottom shelf. When loading plants onto trays, employees at Zuydgeest or Oriental Group manually enter a description of the order in the van Plant tot Klant system, linking that description with the ID number on the tray’s tag and the trolley tag, after which the tags are printed on an RFID label printer and stickered on the trays.
As the trolleys are loaded onto trucks destined for Sierteelt Direct, they pass through a Motorola RFID portal (each portal consists of one reader and eight antennas—four on each side of the dock doors), capturing the IDs encoded to the trolley and tray tags, and transmitting that data via a cabled connection to Interaxi’s software, which links each ID number with a date and time stamp. Interaxi’s software platform uses Microsoft Silverlight for the user interface, and Microsoft BizTalk Server RFID 2009 for the storage of and access to information on Interaxi’s own server.
The Interaxi software compares the products on the trolley with the order destined for Sierteelt and displays a list, along with any discrepancies, on a screen mounted above the grower’s dock doors. At the same time, the software updates the order’s status, indicating what has been shipped, and when. In that way, Sierteelt can then access the server and determine when the trolleys were shipped, and thus when they could be expected to arrive.
When the shipment arrives at Sierteelt Direct, the trolleys pass through another Motorola portal (there are two at the site—one for incoming trolleys, and another for outgoing), updating the system to indicate the order’s receipt. The trolleys are coupled together and then moved through the second (outgoing) portal via a tractor, thereby updating the system that Sierteelt has loaded specific orders onto a truck bound for Hamiplant. Although in the case of the pilot, all tagged product trays are being shipped to Hamiplant, if the RFID system were expanded to include other exporters, Heemskerk says, a screen above the portal could warn a tractor driver if there was a discrepancy—such as a trolley being loaded onto a truck bound for the wrong exporter.
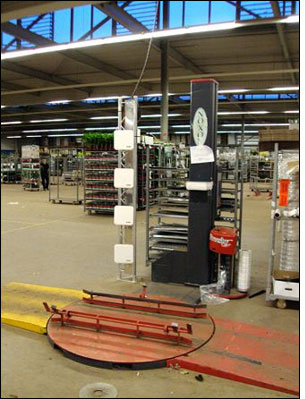
At Hamiplant, the trolleys are typically unloaded and repacked to match retailers’ specific orders. Therefore, Interaxi installed three portals: one at an incoming dock door, one in the repacking area and another at an outgoing dock door. As the tags pass through the portals, the status of the trolley and its trays is updated in the system software, and made available to interested parties in the supply chain. As the items are unloaded and repacked, specific orders are linked to the RFID tags on each tray, and the software compares the order against what should be loaded onto the trolley, thus ensuring the order is correctly filled. The trays are then linked to the new trolley’s RFID tag.
At Hamiplant’s outgoing dock door, the trolleys are loaded onto trucks operated by Breewel Transport, which installed RFID portals at two of its facilities. One portal is located at Breewel’s distribution center in Hazeldonk, the Netherlands, from which orders are delivered directly to retailers. The other is located at Breewel’s Paris DC, where trays are unloaded and then reloaded onto smaller trucks for delivery to stores in the vicinity. Once the tagged trays and trolleys leave the Hazeldonk and Paris DCs, the RFID-based tracking process is completed, since the tags are not being read by retailers.
The group encountered several obstacles with the pilot. For example, they chose not to tag individual plants, speculating that doing so would be too expensive for participants. In addition, the metal in the trolley created some challenges for reading the RFID tags on the trays, since it interfered with transmissions. Heemskerk says the participants attached the tags at a spot on the tray at which it could not come into contact with the trolley’s metal bars.
The pilot is expected to be completed in the last quarter of this year, Heemskerk says, after which participants will evaluate the results and complete a report by early 2011, indicating how successful it was. The main benefit, he notes, has been to reduce labor hours for the supply chain participants (the number of bar-code scanning events, for instance), and to catch shipment errors. It has also enabled Sierteelt Direct, Hamiplant and Breewel to better forecast when shipments would arrive and, in that way, to staff the warehouses accordingly, as well as schedule other tasks around the product’s expected arrival time.
What’s more, Heemskerk adds, because the participants can better schedule their staff’s loading, unloading and repacking tasks according to shipment arrival estimates, the companies have been able to optimize their logistical processes, making surprise surges in order arrivals less likely to occur. The system has reduced errors by alerting employees immediately if an order being filled contains any incorrect or extra items, or if anything is missing from that shipment.
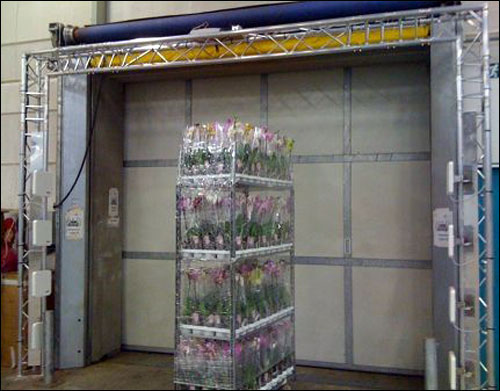
“The project has been very successful,” Heemskerk states. “I think we can yield a lot of benefits with RFID.” Interaxi’s full report on the pilot’s results will be reviewed by Florilog and the supply chain pilot participants, in order to determine whether to proceed with a permanent RFID deployment.
Other horticultural companies and organizations have deployed—or are attempting to deploy—radio frequency identification. Since 2002, Dutch flower-auction cooperative FloraHolland has been utilizing various RFID applications to track trolleys of flowers, and to more efficiently move products through its facility (see Dutch Horticultural Company Sends Flowers via RFID).
For the past two years, horticulture logistics supplier Container Centralen has been working to apply EPC Gen 2 RFID tags to all 3.5 million of its plant trolleys (or CC Containers) in Europe, as part of an effort to better control its inventory, as well as reduce shrinkage and counterfeiting (see Container Centralen Says It’s Ready to Roll Out RFID in Europe). The firm originally set a deadline of Feb. 1, 2010, by which all of its plants trolleys would be tagged, but in response to requests for additional time from its customers (various members of the horticultural supply chain), the cut-off date was postponed to Nov. 1 of this year. Recently, that deadline was extended again, to Jan. 10, 2011.
Separately, in the United States, Container Centralen is employing active RFID tags on 250,000 of its trolleys, so that they can be tracked at 150 locations throughout the country (see Container Centralen Adds Active Tags to U.S. Carts).