Managers at the Diablo Canyon Power Plant (DCPP) know exactly where the plant’s back-up equipment (used to maintain two reactors) is, even if it hasn’t been utilized for five years or more, thanks to an RFID system designed and installed by a team of students at California Polytechnic State University‘s RFID laboratory group, the Cal Poly Laboratory for Global Automatic Identification Technologies (PolyGAIT).
The group, led by industrial and manufacturing engineering professors Tali Freed and Larry Rinzel, who serve as PolyGAIT’s directors, installed the system for the nuclear facility’s warehouse approximately one year ago. Mike Krist, a graduate student and the project lead, interned at DCPP. Krist developed the software and its required reports, and integrated the RFID system with the plant’s existing back-end system. Since then, says Del Ritchie, DCPP’s supply chain manager, the facility has increased accuracy, reduced the time employees spent taking inventory of its entire warehouse from 2,000 labor hours down to just 300, and decreased the time workers spent searching for missing items from several days to a few minutes. Based on that success, the power plant’s tool-management group is also preparing to install an RFID system later this year, to track the tools that enter and exit its tool room.
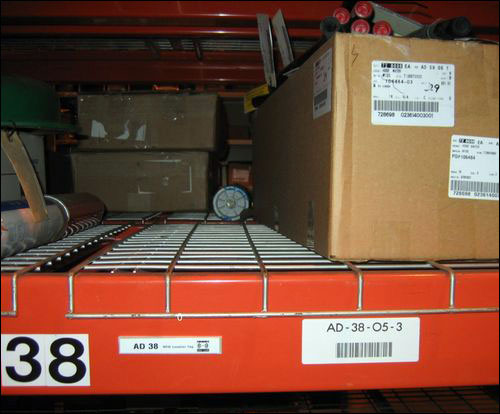
PG&E, the California utility company that runs the Diablo Canyon site, first began looking into RFID technology at the PolyGAIT lab in 2008. PG&E maintains a close relationship with Cal Poly, partnering with the college for engineering services, for example. “They had the RFID lab, and we had seen their scanning and reading capabilities and asked, ‘Is there something we could do with that?'” Ritchie says. “We had to think a while, and determine how to use the technology with a reasonable ROI.”
PG&E decided that RFID would be best utilized at its DCPP warehouse to track some of the 70,000 pieces of back-up equipment for the two nuclear reactors. About 40,000 of those assets are considered “just-in-case” items that are unlikely to be used, but are critical to have on hand. Many of them are highly specialized, so if a piece of equipment on a reactor fails and the proper replacement is not immediately available, the reactor would have to be shut down until an alternative item was located or built.
With RFID, Ritchie hoped the warehouse would have greater visibility into what is on hand at any particular time, when equipment needs to be maintained, and where it is located. The facility has a 100,000-square-foot warehouse, with $100 million worth of inventory, and each piece of equipment must be inspected every two years. “We decided the best option was to put tags on the inventory items that don’t move,” Ritchie explains. Those 40,000 items consume large amounts of staff time spent counting and ensuring the assets are in hand and in proper working condition. “We don’t expect to use them, but they’re priceless if we need them.”
Most inventory counts take place during a refueling outage, when a reactor is taken off-line to be refueled. The outages occur every 18 months for each reactor. In 2009, one reactor underwent a refueling outage in February; the other, in October. When a reactor is shut down for refueling, all of its parts are checked and maintained to ensure they work properly, with items retrieved from the warehouse, as needed, to replace those deemed to be worn out. Typically, around 10,000 parts are moved from the warehouse every month during a single outage.In the summer of 2008, PG&E began by tagging 20,000 items that were not expected to move in five years, and that were valued at more than $100 apiece. The next challenge was to find the best, least intrusive way of reading those items’ tags without building a large reader infrastructure.
The PolyGAIT solution includes one reader with two antennas installed on each of three forklifts, along with handheld readers to capture ID tags on items stored in drawers. Data regarding the tag reads and the equipment to which they are linked is stored in the software provided by Cal Poly.
Students printed labels containing EPC Gen 2 passive ultrahigh-frequency (UHF) RSI-647 Corkscrew RFID tags supplied by RSI ID Technologies (now owned by Sirit), and attached them to parts (at present, Diablo Canyon’s staff has taken over this responsibility for newly acquired items). Each item is input into DCPP’s SAP enterprise-resource planning (ERP) system, as well as the RFID software, designed by Cal Poly students, and an RFID label is then printed on a Zebra Technology printer and attached to the item, with the unique ID number of the tag linked to the asset to which it is attached. After that item is put away, one of the forklifts transports it to its storage location. There, the forklift’s Sirit INfinity510 RFID interrogator reads the RFID tag on the shelf, as well as the item’s tag, and the software links that shelf RFID tag with the asset’s tag. The antennas are placed on the forklift in such a way, Freed says, that they can capture ID numbers from both low and high shelves. Information is forwarded from the Sirit reader to the back-end software via a Wi-Fi connection.
In addition, every time a forklift passes down an aisle, its RFID interrogator reads the RFID tags on that aisle’s shelves, as well as on the items stored on them, and transmits that data to the software once more, thereby providing DCPP with an up-to-date inventory of the assets. For smaller items stored in drawers made of metal (which can obstruct UHF RFID transmissions), a staff member must remove one antenna from the forklift, open the drawer and read the tags, again using a Wi-Fi connection to send that information to the back-end system. The removable antennas were fitted with handles on their backside for a comfortable grip, Freed says.
The software that captures and interprets the data then provides the location and time of reading for each item to DCPP’s own management software on its ERP system. When specific items are required, workers can run a pick list through DCPP’s management software, which pulls location data from the RFID software. The list can then be provided to warehouse employees, saving time they would otherwise spend looking for specific items.
Additionally, the system was designed to capture irregularities, such as an item being moved from its assigned shelf. For example, if the reader on a forklift making its rounds reads a shelf ID number and an equipment ID number that do not match, it issues an alert to the software, which reports an improperly located asset. To test the system’s locating functionality, Ritchie says he hid three items throughout the warehouse. The ID numbers of the tags attached to the hidden assets were then input into a forklift’s reader. Each time the forklift neared the items in question, the interrogator emitted a beep. “It took 10 minutes to find all three items,” Ritchie says, which could have taken days to track down manually. “That’s a nice side benefit.”Over the course of one year, the time spent on inventory-tracking (including the retrieval of parts during the February and October refueling outages) was reduced from 2,000 hours to about 300. Thanks to this savings in labor, Ritchie says he expects to recoup the cost of the RFID hardware and software within 18 months of the system’s installation.
Based on the warehouse system’s success, DCPP is also deploying an RFID solution in its tool room. The tool-tracking system, designed and installed by PolyGAIT, is expected to be in full operation at the end of 2010 or early 2011, says John Gutierrez, the nuclear plant’s tool-management group supervisor.
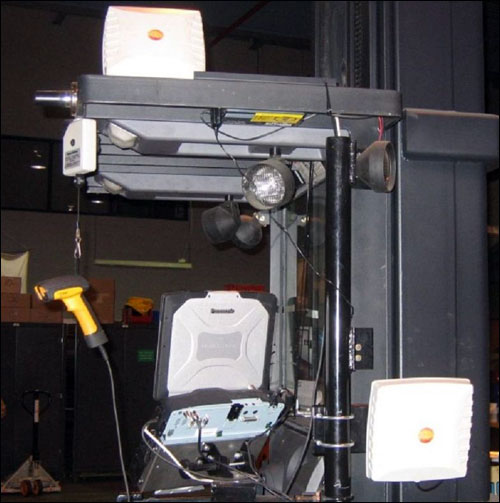
“We have had some occurrences where M&TE [maintenance and test equipment] is removed from our tool room, by unknown users without documentation,” Gutierrez says, adding, “I am hoping to be able to track who took the M&TE, as well as what piece of M&TE was removed from the area.” Typically, M&TEs are used around the clock, but the tool room is manned only during the day. After hours, the room is still accessed by staff members who need tools, and they manually record the items they are taking on a piece of paper. With RFID, Gutierrez hopes to set up a system that automatically tracks which personnel check out which tools, thereby eliminating the need for employees to use pen and paper, and preventing occurrences of undocumented M&TE removals.
Staff members will wear badges containing RFID tags, with an ID number encoded to each tag that links to the identity of the employee in the stand-alone RFID software being provided by PolyGAIT. Then, if a worker takes tools that are needed and walks out the door, a reader portal would capture the ID number of the employee’s badge, as well as that of each tagged tool as it exits the tool room. The software would then update the tools’ status as “checked out,” and link those items to the responsible party. The system should reduce shrinkage, Gutierrez says, “which is a cost savings. And it should reduce labor spent retrieving tools, because we should know if something is in the tool room—and, if it’s not, who has the tool.”
The system, using Xerafy PicoX tags and Sirit readers, has been tested in the PolyGAIT lab, but not yet in the DCPP tool room. Xerafy’s PicoX tag, Freed says, proved to be the most durable UHF tag, with the most reliable performance. According to Freed, the tag is encased in a capsule to withstand the harsh conditions at DCPP. Students will attach the tags with tape or zip-ties.
In addition, DCPP’s Foreign Material Exclusion Group (which works to ensure, for safety purposes, that everything that enters the reactor room is ultimately removed) is working with Cal Poly to develop a system whereby the company can automatically monitor which personnel enter a reactor area with which tools, and ensure they exit with those same items, rather than leave something behind that could pose a hazard. That system has not yet been piloted, Freed says, though a prototype has already been designed, and is slated to soon be tested at the PolyGAIT lab.