Saturdays are busy days at the Federalsburg, Md., cross-docking distribution center of H&M Bay, a national less-than-truckload (LTL) carrier of frozen and refrigerated goods. Late in the day every Friday, the company’s fleet of 130 or more trucks begins arriving with trailers loaded with beef, seafood, bakery items and other temperature-sensitive goods.
To improve on its system of transferring freight from one truck to another, the company decided in 2008 to install cold-storage rooms so freight could be unloaded and stored in a temperature-controlled fashion until it was ready to be loaded onto another vehicle. However, the firm also realized that if it installed such cold-storage facilities, it would require an RFID-enabled system that would allow it to locate products in those rooms quickly, and to track the length of time each product has been in and out of cold storage, as well as when it shipped. Now, nine months after launching its new cold-storage operations, the company has concluded that the RFID system has successfully fulfilled those requirements, says John Walker, H&M Bay’s software development manager.
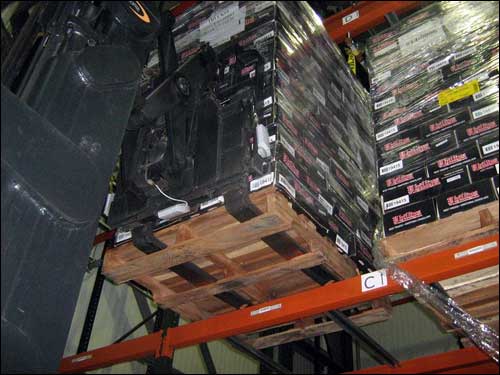
Prior to deploying the RFID system, Walker says, H&M Bay had met with supply chain software system provider Franwell, and liked the company’s approach. Walker’s team had specific demands of the RFID system it sought. “I need to make sure I can find every pallet,” he explains. “I need to be able to quickly go and find it.” H&M also wanted the system to be relatively unobtrusive, he says, noting “Our workforce is all on forklifts. This thing [RFID system] had to be mobile, and it had to be done quickly. Now that we have this nice cold-storage facility, we have to get the product into it quickly.”
Franwell indicated it could design a system to meet those constraints, and the two companies began working together to formulate a solution. The result is a system in which pallets are fitted with passive ultrahigh-frequency (UHF) Gen 2 RFID tags, then stored on racks fitted with similar tags. The pallets remain in those tagged racks until an order is placed, at which time they can be taken out of cold storage and moved to a loading dock, while H&M Bay tracks data regarding all of those movements.
The racks can be up to 40 feet tall, well out of arm’s reach, Walker says. As such, a UHF RFID system, with a mobile reader mounted on the forklift, proved to be the most effective solution. The company also has a reputation of staying on the cutting edge of business practices, he says, and using RFID provided that much more advantage over the firm’s competitors.
The system was custom-designed to be user-friendly, according to Terri Crawford, Franwell’s VP and COO. “We couldn’t build a complex inventory system with a complex user interface,” she states. H&M’s employees typically move quickly on forklifts, often working weekends—and many are part-timers—so the system needed to be intuitive and require little operator training.
When a shipment arrives, the warehouse staff logs its receipt data on a PC in the warehouse. The employee then prints two passive UHF Gen 2 RFID tags, both encoded with an identical ID number using Franwell software in conjunction with a Datamax H Class DMX-1-4210 printer-encoder. One tag is applied to the front of the pallet so that a forklift interrogator can read it, and the other is applied to the top of pallet, so that it can be read by a portal interrogator. The Franwell software then passes the tag’s ID number to H&M’s back-end system, where that ID number is linked to the shipment receipt data, as well as the time and date. The pallets are then transported to a staging area.
Tagged cold-storage pallets are picked up from the staging area by one of three forklift trucks equipped with a Motorola RD 5000 reader, to be taken into cold storage. The truck’s interrogator captures the pallet tag’s ID number, then transmits that information to the forklift’s VC 5090 onboard computer, which sends it along to the company’s back-end operating system via a Wi-Fi connection.
There are two portal RFID readers at the refrigeration unit doorway, as well as one at the freezer, all of which capture each pallet’s tag ID number once more, then forward that data to Franwell’s AssetTracker software service via a cabled connection. The software service determines which pallets enter or exit cold storage, then transmits the movement data to H&M Bay’s operations system. Each of approximately 1,600 rack locations in cold storage is marked with an RFID tag, so that when the forklift driver places the pallet onto the rack, the reader captures the rack tag’s ID number and the system maintains a record of the pallet’s exact storage location.
When a pallet is removed from a rack, its tag is again interrogated by the forklift’s RD 5000 reader, followed by the portal readers. The system can then determine that the product has been removed from cold storage prior to being loaded onto a truck.
Deployment of the system began in March 2008, Crawford says, and was completed in August after the system was tweaked for better read rates and the hardware was adjusted. According to Walker, the system allows the freight to be unloaded earlier than was previously possible, and to be held in storage until a truck could transport it to the retailer. It also enables the company to provide data to shippers indicating how long the freight remained in and outside of cold storage.
H&M Bay hopes to install the technology at its facilities in North Carolina, Massachusetts, Washington and Florida. At present, however, no dates have yet been set for such deployments.