To help quickly locate spools of electric cable stored at its warehouse, Italian cable wholesaler Sada Cavi has deployed a system combining radio frequency identification with ultrasonic height sensors.
Sada Cavi markets a variety of cable products, with reported annual sales of €40 million ($63 million). The company stores up to 40,000 wooden spools of electric cable in its storage yard near the city of Modena. Each spool is unique, since the length of leftover cable differs from one spool to the next. One key success factor for Sada Cavi has been in eliminating wasted cable on spools by using the correct spool to fill a specific order.
“The company makes money by not wasting too much cable,” says Korbian Sapper, a member of the sales and marketing department at Indyon, the German company that supplied the RFID system to Sada Cavi. “This is the trick—minimizing residual cable.”
Before switching to RFID, Sada Cavi spent a good deal of time locating the ideal cable spool for production, in rows stacked four spools high and 20 deep in a yard measuring about 20,000 square meters (215,000 square feet). Following production—during which Sada Cavi tailors the length of cable for each particular customer—every cable order must be identified for shipping as well.
At the end of 2005, Sada Cavi contacted WeFlex—an Indyon partner in Maranello, Italy, that offers logistics services and solutions—regarding a solution to the problem. Sada Cavi has some automated indoor high-rack storage units, and considered building more but ruled that out due to the cost involved.
Sada Cavi also contemplated utilizing the bar-coded labels it initially applies to products or product pallets for identification at every step of the process. Small cable drums are transported on pallets, while large cable drums are moved without them. The company eliminated bar-coding as an option, however, because of the outdoor environmental conditions: When a plastic-covered bar-code label is wet, or if the sun shines brightly on it, reflected light can interfere with reading. The firm also shied away from bar codes due to the time it would take to scan them. Sapper estimates 20 to 30 seconds per scan would be required with forklift-mounted bar-code readers, and each of Sada Cavi’s forklifts must identify spools approximately 800 times per day.
WeFlex developed the new warehouse layout and processes, and designed the final customer-specific processes at Sada Cavi together with Indyon. It also installed parts of Indyon’s Track+Race forklift-tracking application.
In 2006, Sada Cavi began implementing its RFID system, which features 2,000 passive 134 kHz RFID transponders embedded in the concrete pavement at key junctures in the yard, as well as four forklifts—each outfitted with an RFID antenna, a height sensor, an RFID interrogator and an onboard computer known as a control unit. The sensor and interrogator are connected to the onboard computer, and information collected is transmitted to the warehouse management system, also from Indyon, via WLAN.
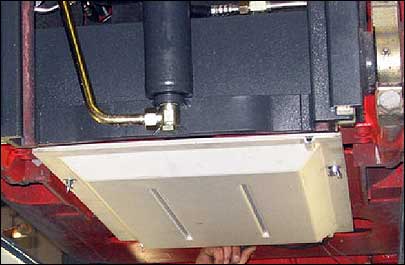
When a truck filled with spools arrives at the warehouse, workers unload them, applying a bar-coded label to each, then place them in a dedicated storage area also outfitted with RFID tags in the pavement. A forklift driver picks a spool from this area, and the system instructs the driver to identify the spool just loaded by scanning its label’s unique bar-coded ID number. The system then has the basic information required to track the spool. This is the only time the bar code is read.
When an order needs to be filled, a forklift driver enters the cockpit and receives instructions on the control unit’s touch-screen monitor regarding which spools to pick. The system knows which spools are stored in which bins at which levels, and sends the driver an appropriate message. He or she drives the forklift to the correct bin, crossing multiple RFID tags embedded in the pavement along the way. With each crossing, the antenna beneath the forklift reads the tag’s unique ID. This information is sent to the control unit and on to the warehouse management system, where the real-time location of the forklift is calculated.
As the driver begins to unstack and restack spools while searching for the proper one, an ultrasonic sensor on the forklift measures the height of the load. This sensor can also detect if the forklift is empty. By combining the ground location, supplied via RFID, with the height information, provided by the sensor, the system can determine which spool is being moved, and where it is placed. “One main challenge for the Track+Race system,” Snapper says, “was to detect automatically the loading event, no matter how the cable drum is loaded by the forklift truck—with or without a pallet—and considering the different orientations of the drums.”
A work order remains on the screen until a driver has successfully picked and delivered the intended spool to the appropriate destination, such as a production or shipping area. In the case of production, the system issues an order to transport a specific spool to a particular production machine for tailoring the cable. The warehouse management system knows the location of the spool in the warehouse and generates the transport order for the forklift truck. In the event that the entire spool is sold and no production is necessary, Snapper says, the system orders that the spool be taken directly to the shipping area.
Indyon designed the system with 134 kHz passive tags, complying with the ISO 11784 and 11785 standards, because they are small and well-adapted to the outdoors, where tags may be covered by snow, ice, water or rain. Indyon declines to name the tags’ manufacturer, but indicates it to have been a well-known company in the United States. Each tag is contained in a plastic housing and is about the size of the narrow end of a golf tee—3 centimeters (1.2 inches) in length and 3 millimeters (0.1 inch) in diameter.
Sada Cavi uses electric forklifts from Still, which Snapper says generate a large amount of electronic smog (electromagnetic radiation). That’s why Indyon customized the RFID interrogator’s antenna by adding a protective layer to the inside of the case to keep out RF and magnetic interference. Antennas are mounted underneath the vehicles.
“The antenna has to be very robust and protected against temperatures as well,” Sapper says, adding that Indyon designed the antennas specifically for use on forklift trucks so they would be operational despite the electronic smog. The interrogator, supplied by Texas Instruments, is connected to the control unit, also designed by Indyon. Both the RFID reader and the control unit are located in the forklift cockpit, away from moisture, dust and humidity.
While implementing the system, Snapper says, Sada Cavi trained workers on its use. “Drivers have to understand the business process,” he explains. “They can’t just place spools where they want.” He says Indyon had no problem implementing the RFID component of the solution, but spent time adapting the system to the enterprise resource planning (ERP) system used by Sada Cavi.
After the six-month rollout, Sada Cavi hired WeFlex to add three additional RFID-enabled forklifts, and to expand the number of identification points in its yard by drilling a small hole in the pavement, inserting an RFID transponder into that hole and programming its unique ID number into the computer system. Sapper says the system has a 100 percent read rate, and that it has decreased many times over the time required for Sada Cavi to locate and transfer spools.