The more than 7,500 employees at St. Olavs Hospital, a large health-care center in Trondheim, Norway, treat approximately 50,000 patients annually. To support its massive staff and operations, the hospital owns and maintains more than 130,000 work garments, including operating gowns, robes and scrubs.
As part of the facility’s massive reconstruction efforts over the past few years, it has deployed an RFID-based uniform-tracking system offering real-time inventory visibility of its uniforms. The company says this has led to savings in inventory space, labor and operational costs. Texi, a Norwegian textile management solution provider, designed and deployed the system for the hospital using passive 13.56 MHz RFID tags from Texas Instruments’ (TI) and readers made by Feig Electronic. The tags, which are sewn into the garments, comply with the ISO 15693 and ISO 18000-3 standards.
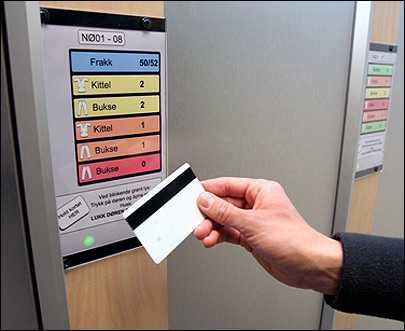
Under the old system, the hospital used a paper-based tracking system to ensure each ward was continually stocked with enough clean garments—in the appropriate sizes—for each staff member during every shift. However, this manual system sometimes suffered from inaccuracies that left employees scrambling for clean uniforms before their shifts. It also required valuable staff time to fill out the forms—an inefficient use of labor. Moreover, because the garments were stored on hangers and moved on a conveyor system between the laundry and storage facilities, this required substantial space inside the hospital.
The new system started as a pilot project in 2005 and has been fully deployed since September 2006. Employees use their RFID-enabled personnel badges, which operate at 125 kHz, to open uniform storage closets containing the uniforms they need on a given day. A 125 kHz reader is linked to a lock that disengages after calling up the employee’s identity, based on the ID encoded to the personnel badge, and verifies that the employee has access to the uniform closet.
When the employee removes the uniform items needed for a shift and closes the closet door, this engages the lock and triggers the 13.56 MHz Feig Electronic reader, also inside the closet. The interrogator takes a reading of the closet’s contents, using antennas mounted on each shelf to read the tags embedded in the stored uniforms and update the inventory.
When uniform stock falls below a set level, the system sends an alert over the hospital’s uniform inventory software, ensuring that the staff replenishes the shelves before letting them fall empty.
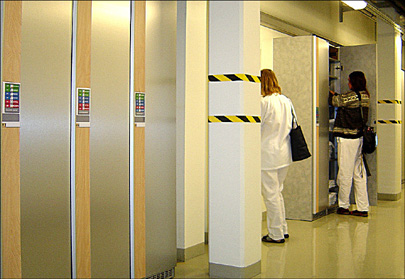
Each employee places used uniform items in a bin designated for soiled laundry. As the items are placed in the bin, a reader mounted inside it is trigged to read the tags. The interrogator then sends the garment IDs and a time stamp to the back-end software, which updates its records to show that those particular garments have been submitted for laundry and are no longer in the possession of the employee who removed them from the closet.
The software also notes the hospital ward in which each employee works, enabling accounting records to charge the ward accordingly for laundry services.
The circular tags are enclosed in a rugged, seamless plastic casing, a process known as overmolding, to help them withstand the high temperatures and pressures of industrial laundering. Each tag has a small profile at 22 mm in diameter and tag holds 2 kilobits of rewritable memory. (Texas Instruments has also just launched a 256-bit memory version of the tag, designed for applications that do not require a full 2 kilobits of memory.)
According to Texi founder Vidar Kvalheim, the results of the St. Olavs uniform-tracking system have been very positive. Kvalheim says the hospital expects to save several million Norwegian kroner each year through improved inventory accuracy and labor reductions. Since the new system required 90 percent less space than the old system (which was housed in an older, now defunct facility), it has already saved an estimated 40 million kroner ($6 million) in space savings.