Managing the risks and opportunities related to asset operations for industrial companies is not new. Companies have processes to try to optimize inventory and logistics, and to put measures in place to minimize outages, but the effectiveness has been limited. Why have these efforts been ineffective? There are a few reasons: traditional data sources often have quality issues, while reactive analytics has been mostly limited to reporting historical information or generating alerts only when one data point goes over a set threshold, just to name a few examples.
As stagnating industrial productivity persists, companies have been compelled to re-examine the overall effectiveness of asset operations. The emergence of the Industrial Internet of Things (IIoT) is bringing a new perspective and rewriting the book on asset performance and efficiency. Companies that leverage this technology will outpace performance inflation and stay ahead of the competition.
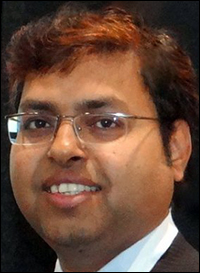
Using the Untapped Potential of the IoT and Smart Use of Heavy Industrial Assets to Improve Operations
Often, the assets that can contribute more than half of an industrial company’s total asset base hold the key to both opportunities and operational risks. For example, if a critical 2,000-barrel-a-day pump at an oil company goes down with oil priced at $100 a barrel, a company can lose $200,000 daily because of a single piece of faulty equipment. Industrial companies need to ask themselves how the new IIoT model can help to prevent these systemic vulnerabilities.
Combining New Digital Technologies and Intelligent Processes
Traditional models have been rigid, inflexible and non-optimal in dealing with the asset lifecycle. The IIoT brings a whole new perspective and expands the possibilities for asset performance, by leveraging an additional smart player in the mix—smart assets that combine with new digital technology and intelligent processes.
Possibilities range from increasing effectiveness with sensors that better connect the performance of various assets, to doing things differently by using that connected data to streamline and improve processes. Companies can also launch a new set of business models, such as developing additional revenue from new aftermarket services. The IIoT helps industrial companies to completely reimagine outcomes and opens doors to huge untapped potential in asset operations.
Using Existing Data More Effectively
Industrial companies sit on a mountain of data but struggle to draw insights from this information because data collection often occurs in silos leveraging disparate systems. Aggregation, synthesis and analysis happen with extensive manual intervention, which compromises the agility, quality and timeliness of the insights.
IoT-based systems force the disparate sources to converge, and amplify the quality by seamlessly aggregating real-time data from the assets and removing the need for manual interventions. As a simple benefit, IoT-enabled operations help users to monitor assets better with greater granularity, which alerts companies to trigger events with better accuracy. This also tracks fleets with improved precession, helps better monitor asset performance and drives insight for better control.
Connecting Smart Assets With the IIoT to Drive Better Insights and Predictive Maintenance
With connected smart assets and the IIoT, organizations can reimagine the assets as an integrated pillar of strategy and operations that is both a source and a consumption point for information. Connected assets can trigger insights to help predict failure, and hence decide the need for critical spare parts.
The possibilities are endless—inventory management becomes a dynamic insight-based procurement for inventory optimization; condition-based monitoring can provide real-time insights to dynamically plan for field force optimization; and operational insight can combine with environment and context to decide control actions for performance optimization.
Despite the Possibilities of Smart Assets and the IoT, Challenges Still Remain
While the untapped potential of the IoT in the industrial world has delivered meaningful progress, companies face innumerable challenges. Organizations often over-focus on technical aspects of solution deployment and are biased to over-focus on connectivity and en-masse data collection, while the crucial upstream part of how to best leverage results in new ways is postponed to the mythical later phase.
Often, research and development teams have high expectations for data collection and are thus disappointed when the data arrives to the cloud and only a fraction of it can be utilized for value. By utilizing smart data in real time, connected more through asset-management process, the IIoT brings discipline to ensure value-realized aligns with value-envisioned. Business case takes the precedence. IIoT projects work best with an outcome-centric approach coupled with design thinking, which applies new-age technologies in the context of a domain to create tangible impact for sustainable competitive advantage.
Smart and connected assets create the base for innovation by design. Intelligent assets feed the information to perform advanced analytics for original equipment manufacturers (OEMs) to better control the product lifecycle, which helps with innovation because owner-operators can sell outcome instead of service. They can create entirely new business models linked to outcome, enabling a fundamental shift in business models geared toward the consumerism trend in the business-to-business world.
Sukant Acharya is the VP of sales for high technology, manufacturing and services, and the global head of IoT business, at Genpact, a global professional services firm focused on delivering digital transformation.