Trivilita, a 10-year-old bedroom furniture manufacturer based in Šiauliai, Lithuania, reports that it has increased the accuracy of its orders to nearly 100 percent, by deploying a radio frequency identification solution at its facility that tracks which goods are being loaded, as well as for which customer, and also alerts a vehicle’s driver before a mistake can be made, via RFID pallet tags and reader portals at its dock doors. UAB Autepra provided RFID hardware and consulting services for the deployment, while Trivilita itself installed the technology and created its own software to integrate with the firm’s existing enterprise resource planning (ERP) systems.
The company produces beds, mattresses, quilts and pillows for retailers that sell the products throughout the world, and IKEA is one of its largest customers. Quick response to high-volume orders is essential to the company’s clientele, but the movement of a high volume of goods can quickly lead to errors. Therefore, Trivilita installed the RFID solution in September 2012, with the goal of improving efficiency by reducing the amount of time employees spend scanning bar-coded labels at the loading dock, as well as preventing mistakes as trucks are loaded with orders. The company is now utilizing the solution to track 5,000 to 6,000 pallets loaded with merchandise as they leave the warehouse each day for delivery to customers’ stores.
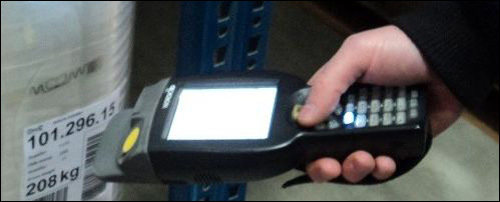
Prior to Trivilita’s adoption of RFID several months ago, the company’s warehouse-management system depended on bar codes to track goods as they were manufactured, stored and shipped to customers. Its customers demanded that a bar-coded label be attached to every pallet loaded with goods, Trivilita reports, and it had been able to use those labels to its own advantage, by scanning each one’s bar-coded serial ID number as the pallets were loaded with goods at the end of assembly lines, again as they were moved into storage and then once they were shipped. Scanning each bar-coded label, however, was a time-consuming task. In addition, the company sought a way to provide order and product location data to forklift drivers, in order to make the delivery of goods to the dock doors more efficient. Thus, the firm chose to install an RFID system, and to mount mobile computers on forklifts so that the vehicles’ drivers could view data related to orders and RFID reads at the dock doors.
The Lithuanian company was not ready to discard the bar-code tracking solution, however, so it installed a system using its own software that enabled the use of both bar-code and RFID labels attached to every pallet, each with an identical number. The company not only began applying RFID tags to every item, but also installed a CAEN RFID R4300P-ION fixed RFID interrogator at each of its two dock doors. In addition, it mounted computers onto forklifts, with a Wi-Fi connection to the warehouse-management software, to display order and location data.
Trivilita moves pallets of products through a 5,600-square-meter (60,300-square-foot) facility—with the exception of beds, which are not placed onto pallets. The company plans its production of goods in such a way that it can maintain the inventory levels required by its customers—large retailers that need to ensure that when they place a large order, the appropriate products will be immediately available for shipment.
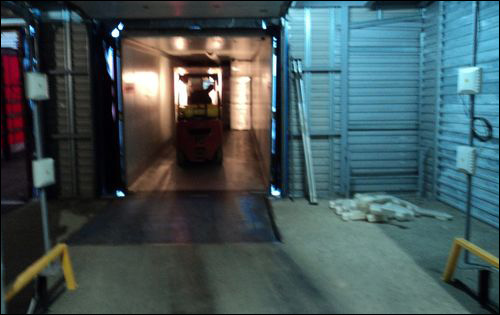
While the bar-code system made it possible to know how much of a particular product was on hand at any given time, the bar-code scanning process proved disruptive for workers. “The forklift driver must step off [his vehicle] in order to scan pallets,” says Andrius Vilciauskas, the company’s deputy director. What’s more, the process provided the company with a 98 percent shipping accuracy rate (approximately 2 percent of shipped orders were missing goods or contained incorrect items), but management wanted to get that accuracy rate even higher.
To increase accuracy and reduce time, Vilciauskas says, “an RFID solution using fixed readers in shipping area seemed very attractive and more productive.” Trivilita was already aware of RFID, he notes. Its sister company, Artilux NMF, was already using RFID technology from UAB Autepra (see RFID Illuminates Lithuanian Lamp Manufacturer). Trivilita met with UAB Autepra to purchase the necessary hardware, including all tags and readers, says Tomas Girdzevicius, UAB Autepra’s director. However, he notes, what was unique about this project was the involvement of Trivilita’s IT department, which created its own software and middleware to receive, store and manage RFID read data. Trivilita also installed the hardware itself, with Autepra offering consultation services as necessary.
After newly assembled goods reach the end of the assembly line and are packed onto a pallet, the loaded pallet is then stretch-wrapped and a bar-coded label, encoded with a unique ID number, is applied to the wrap. The bar-coded ID is scanned via a handheld reader, thereby indicating that the item has been produced and palletized. (Some mattresses and beds do not fit on pallets, and those bulkier items are not tagged.) The order is then transported via forklift or hand truck to the warehouse area, located in the same building. There, staff members use a Nordic ID Merlin ultrahigh-frequency (UHF) RFID reader to first scan the bar-coded number on the pallet’s label, and encode that same ID onto a Smartrac ShortDipole EPC Gen 2 passive UHF RFID tag that is then applied to the pallet.
At this point, the warehouse-management software is updated to indicate that the item has arrived at the warehouse. Once the goods are placed in storage, a worker reads the tag once more and scans the ID number of a bar-coded label attached to the shelf, in order to link that product with a specific shelf location. When conducting any additional inventories, or to search for specific pallets, workers utilize the Nordic ID handheld.
When Trivilita receives a customer order, that request is sent via a Wi-Fi connection to the forklift operators’ computers, which display the items that need to be picked, the shelves where those goods are stored and the dock door to which they need to be moved. Once the drivers retrieve the goods, they pass the dock door RFID reader, which interrogates each pallet’s tag ID number and forwards that information to the back-end software, which then determines if the IDs match those listed on the order. In the event of a discrepancy, the forklift driver will see an alert on the vehicle’s computer, and management can also receive a message alerting them to the problem.
Trivilita built the software using Grails 2.0 open-source Web application framework. It not only links the RFID label each pallet’s bar-code ID, but also stores data related to what is packed onto the pallet, as well as that pallet’s movements, including to the warehouse and dock doors, when it was shipped and to whom. The software integrates with Trivilita’s existing MS Dynamics 5.0 ERP system.
Shipping accuracy, Vilciauskas says, improved from an initial 98 percent to 99.94 percent during the three months following the deployment. “This is a significant improvement for us,” he states. “Our warehouse manager thinks that such a system is a must for any production company.”