- Graphene’s Benefit for the Internet of Things
- Creating Graphene without the Impact of Mining
- Graphene Makes a Blacker Black for High-End Cars
- Potential for IoT Includes Printed Electronics, Sensors
Clean energy manufacturer HydroGraph Clean Power has developed a process for creating graphene, as opposed to the traditional process of mining it from graphite, which the company says makes it more affordable and consistent. The production process, for which HydroGraph has obtained patent rights, uses acetylene and oxygen, which creates graphene when sparked. HydroGraph says it has global exclusive rights to this process.
The company has developed modular production cells in which the material will be made, and it plans to incorporate these units for its customers at their sites. HydroGraph will integrate the graphene production into customers’ existing production system so that they can create graphene and build it into paints, lubricants, adhesives or other materials to make them stronger, more flexible and more conductive, with greater wear resistance.
Graphene’s Benefit for the Internet of Things
Internet of Things (IoT) products could benefit from graphene as an additive to existing materials used in tags and sensors, though HydroGraph says this has not yet been done in commercially available products. There is an application for it in printed RFID tags and IoT sensors, the company notes, since graphene is much stronger and more conductive than other materials, with sensing capabilities.
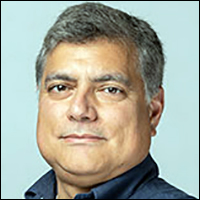
Stuart Jara
In fact, the material has been tested as a biosensor to detect environmental conditions, such as the presence of liquid, chlorine or a temperature change. It also offers electrical conductivity, making it potentially beneficial for products in energy storage, solar cells and medical devices. Graphene can enable printed electronics on a piece of plastic to be bent or folded and continue to operate, HydroGraph reports, and the company is seeking partnerships with technology providers to incorporate its graphene-producing system into existing IoT or RFID materials or product manufacturing.
Graphene has been in use in limited quantities for more than a decade. It is considered a super-material that traditionally consists of an atom-thick graphite sheet. It is stronger than steel and harder than a diamond, according to HydroGraph, and it typically can be chemically combined with other products, providing a superior material based on strength or bonding process. When incorporated into ink, it creates a conductive ink that could be used for printed electronics.
HydroGraph’s founders came across research at Kansas State University and became intrigued with graphene. They then developed a process using detonation technology intended to make graphene more affordable and reliable. “The original founders were just wowed by graphene—it can be a wonder material,” says Stuart Jara, HydroGraph Clean Power’s CEO. “It can make things 20 times stronger than steel, while also being conductive and malleable.” The company thus took on the challenge of finding a better way to produce it.
Creating Graphene without the Impact of Mining
One challenge related to graphene use is the costly process of extracting a layer of graphene out of graphite. Following the mining process, Jara says, chemicals are applied, which can require a large amount of energy. The results are hard to control, he adds, leading to inconsistent quality. The company’s founders, on the other hand, offer a process of making graphene that includes acetylene and oxygen, enclosed in a chamber and ignited with a spark to create exothermic energy and an enormous amount of heat.
The process is less expensive and higher in quality, the company reports, without the need for mining, and HydroGraph expects it to accelerate graphene adoption, which to date has been rather slow. The company built its production facility, currently in operation, near Kansas State University. However, Jara says, the projected market demand and interest it has received from customers has shown that a greater production capacity is needed.
The company is thus building more graphene-production units, and it intends to increase the volume by five or six times by having multiple chamber units online by the fourth quarter of this year. The overall goal, however, is to bring graphene production to the site of the material’s end users. “Our cells are compact and modular,” Jara explains, so HydroGraph intends to build production cells close to where the material will be used. They would then contract with each customer to integrate the graphene into their own products.
Graphene Makes a Blacker Black for High-End Cars
Initially, according to HydroGraph, potential users are expected to be those that make high-end lubricants, composites resins, and inks or coatings. Ideally, the company explains, this would involve high-end products such as parts used in the aerospace and automotive sectors.
With HydroGraph’s chemical process, which uses nanocarbons, the results are more consistent than with previous graphene offerings, according to Ranjith Divigalpitiya, the company’s chief science officer, and that leads to a higher-quality product. For example, Jara says, automotive manufacturers have found that some customers value a blacker sports car. Thus, the use of graphene to create a better black paint can mean a higher-value product for paint companies.
When applied to aerospace components, HydroGraph says, its product can make them lighter, more flexible and stronger than other coatings, as well as resistant to corrosion. “It’s more stable,” Divigalpitiya explains. “It’s more controlled.”
Potential for IoT Includes Printed Electronics, Sensors
When it comes to the RFID and IoT industry, graphene can present an opportunity for printable, conductive ink, such as an RFID antenna. HydroGraph envisions a hybrid RFID tag product, for instance, that incorporates graphene to make the electronics more conductive and thus more sensitive when interrogated. The material’s flexibility and strength could make a tag more rugged in some applications. The technology could also be used to create printed electronics for IoT sensors, such as wearable devices, since graphene offers biosensor capabilities.
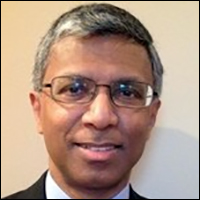
Ranjith Divigalpitiya
The first step for HydroGraph in the IoT market, Jara says, is to identify technology partners that already produce products for that sector. Already, he notes, a biosensor company that has asked to remain unnamed is using HydroGraph’s material to detect specific conditions. By creating a new production process for graphene, Jara says the company has overcome several barriers that have kept the material out of the IoT and RFID industries.
Traditionally, Jara recalls, graphene could not be made with consistent quality and the cost was too high. A third challenge centers around incorporating the material into other materials. “We don’t have to focus on [challenges] one and two,” he states. “That’s done. So now we can spend our energy working with companies to figure out how we can apply the properties of our graphene into their material.”
Jara envisions the material providing sensor-based data that can be captured via an RF or other wireless transmission. The material would require a power source, he says, but it could use the power from an interrogation to send sensor data to an IoT device. “There’s a huge potential there,” he anticipates. Based on a particular application’s needs, he adds, “We can customize [the graphene] to any other host material.”
Key Takeaways:
- HydroGraph Clean Power offers a system intended to make graphene production more affordable and efficient, with more reliable, higher-quality outcomes.
- IoT or RFID technology providers could adopt the solution to improve a device’s strength, flexibility or conductivity.