COVAP, a Spanish agricultural cooperative based in the southern region of Andalusia, is using passive ultrahigh-frequency (UHF) RFID tags to track legs of a premium ham known as jamón ibérico (Iberian ham).
The largest industrial-agricultural cooperative in Andalusia, with reported 2008 sales of €310 million ($444 million), COVAP first began using radio frequency identification in its dairy manufacturing division. After the pilot phase, the cooperative implemented the system that controls the movements of 1,300 pallets per day. The cooperative is now tracking ham from the slaughterhouse throughout the various preparation and curing processes, and may eventually extend the application to track the meat until the point of outbound shipment. COVAP plans to keep the application running for a total of at least three years—the time it takes for one ham to be produced, and the time required to gather a full set of internal data regarding the entire production process.
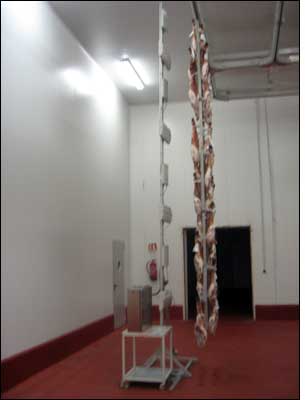
The application got its start as one of the E.U.-funded BRIDGE (“Building Radio frequency IDentification solutions for the Global Environment”) research projects, which aim to speed the adoption of RFID and EPCglobal technologies (see BRIDGE Expects to Launch Five European RFID Pilots This Fall). The COVAP pilot, conducted as part of BRIDGE Work Package 8 (focused on the application of RFID to manufacturing processes), began in November 2008 and concluded in July 2009.
Alexandra Brintrup served as the work package leader at one of the project’s partner organizations, the University of Cambridge’s Distributed Information and Automation Laboratory, at its Institute for Manufacturing. COVAP, she says, was chosen to be the focus of a BRIDGE project because of its previous positive experiences of employing RFID at dock doors to track long-life milk.
The cooperative wanted to expand its RFID application and participate in the BRIDGE project for a variety of reasons: to reduce handling times, enable control of products on a class-by-class basis and trace the production of each leg of ham to comply with food-safety regulations. In addition, COVAP saw the potential for radio frequency identification to help it refine its processes, which involve a large number of ham legs (as many as 300,000 each year) and a wide variety of production variables. By gaining item-level visibility from each production phase, and by mining three years of such production data, COVAP may be able to devise more efficient processes and gain a better understanding of how slight changes in production conditions can affect a ham’s taste and quality.
To produce its hams, COVAP slaughters pigs, cuts them into quarters and then dries and prepares the legs, which are treated, salted and sorted depending on their weight and other factors. A ham production master determines the exact process for each batch based on a variety of factors, including the animal’s original feed and the meat’s PH level. The legs are then aged in temperature-controlled cellars that replicate the original conditions under which the ham was made by hand. Even a slight temperature change can impact the meat’s taste, and the ham master is charged with ensuring the quality of each batch.
During the pilot, COVAP and its technical solutions partner, AT4 Wireless, performed extensive trials before selecting an RFID inlay and designing a suitable tag able to withstand the meat-processing process, which includes burning the ham’s surface to control fungal growth. The testing was carried out at AT4 Wireless’ lab and COVAP’s facilities, where potential tags were tested on the various processes. Germark was eventually selected as the tag provider, and is currently working on an upgraded version of the tag.
As part of the ongoing ham-tracking project, COVAP has already attached the first tag version to approximately 5,500 legs of ham. The cooperative plans to increase the number of hams it tags to the total number produced once the updated version of the tag becomes available.
Initially, the tag had special protective material on both sides. However, COVAP and Germark think the new tag can be designed with this material only on the side affixed to the meat. This, says Santiago Tirado, COVAP’s IT director, could reduce the tag’s cost.
After the pig is quartered and cleaned, COVAP ties the RFID tag to the ankle of the ham leg, and also applies the same sort of bar-coded label on which it had solely relied during its previous ham-leg tracking process. COVAP will continue using bar codes as a backup system indefinitely, Tirado says. “Both systems are compatible, and the bar code does not produce any real extra cost,” he states. “There is no reason to eliminate it.”
A unique ID number is the only data stored on the tags. Further information regarding the ham, including medical information about the originating pig, is kept on a database, linked to the ID number. The cooperative employs a variety of interrogators from Intermec to read the tags at about five different points of the production process. The initial tag reading is performed in the slaughterhouse, directly after tagging. The information is used for inventory purposes, as well as to commence the tracking process. The product then moves along a conveyor through a shaping tunnel, in which the blood is squeezed out. Before the legs enter the tunnel, an RFID interrogator reads their tags. Next, the hams are salted, their tags read once more before that process begins.
“At every read point, we need different antenna types and configurations for the readers,” Tirado explains. “This is not a plug-and-play application. We did extensive trials to select and design the readers. We decided on a combination of near-field and long-field antennas.”
Another read point occurs during what is called the batch-transition phase, in which the ham production master decides where to move hams for further curing, based on several parameters.
In addition, if necessary, COVAP may send hams through a classification machine, which determines the meat’s classification based on its weight and PH levels. COVAP mounted a reader inside a tunnel through which the product moves on a conveyor. Since COVAP operates many cellars for curing the ham, it decided to use a reader it could move from cellar to cellar rather than installing an interrogator at each cellar entrance. That’s why two of the readers are mounted on wheels and outfitted with eight antennas apiece. The interrogator’s eight antennas are mounted onto a 12-foot-tall tower (as tall as a rack of hams), and can be moved along the drying racks, which hold 60 hams each. Read rates averaged between 93 percent and nearly 100 percent. During the testing phase, the lower read rates came from the reader on wheels used at the batch transition point. COVAP was able to increase read rates, however, by rotating the rack on which the hams hung, so that each tag passes by an antenna individually.
“Since we do not have a time restraint during production,” Tirado says, “this shortcoming in the process facilitates reads and keeps us from having to install more infrastructure.”
COVAP used its own software and integrated RFID data into it. Cambridge’s Distributed Information and Automation Lab guided COVAP throughout the project and helped manage the project and develop its business cases and key performance indicators (KPIs). The university analyzed the new process, using special simulation software it has developed for this purpose and comparing it with the former bar-code-based process.
According to Tirado, benefits stem from improved product traceability, which helps it save time looking for items and prevents the need to scrap products not properly tracked. In addition, the company has eliminated some manual scanning processes, thereby saving time and money.
COVAP and its partners trained COVAP’s employees on the new system. According to Brintrup, they gave special attention to explaining to workers that the new technology was not designed to replace them.