A cement factory in southern Turkey has deployed an RFID-based system to speed the weighing and loading of hundreds of trucks per day.
With so many vehicles using the facility on a daily basis, Cimko Cement‘s Narli branch is a busy place. Cimko, a joint venture between Turkey’s Sanko Holding and Italy’s Cementerie Aldo Barbetti, opened the fully automated factory in early 2008.
The company’s management quickly realized, however, that the loading process was a significant bottleneck in the facility’s operations. When trucks entered the grounds, drivers had to exit their vehicles, register with the factory’s staff, receive paper-based lading documents, proceed to scales to be weighed and then move into cement silos for loading—a time-intensive set of procedures, according to Erdal Tokat, a Cimko IT project manager.
Therefore, Cimko decided to adopt a passive RFID-based system to manage the flow of trucks through the facility. The company hired Meyer RFID—a Turkish RFID vendor, and a member of the Siemens Solution Provider program—to help it deploy a system built around 24 Siemens RF600 interrogators with 48 antennas.
“It wasn’t easy to use passive RFID in this environment, because the project is huge,” says Onur Bayindir, Meyer RFID’s general director. The Cimko RFID deployment covers 100,000 square meters (65 acres). While active RFID tags are typically better suited to such a large area, he adds, the €25 ($35) cost per active tag would have been prohibitive in a facility that sometimes sees hundreds of trucks at a time.
Trucks entering the factory now receive a truck ID card containing an Alien Technology ultrahigh-frequency (UHF) Gen 2 EPC RFID tag operating at 866 MHz. The ID cards cost less than €1 ($1.40) apiece, according to Bayindir. The Narli plant keeps 500 cards on hand, in order to handle peaks in demand.
With the new system, the driver no longer must leave his cab. What’s more, a record is created for the truck in the company’s Microsoft SQL database that stores customer information, including the type of cement purchased (packaged or free-filling) and the quantity.
When the truck approaches the factory, the gate opens and the vehicle drives into the facility and onto a set of scales, where a Siemens RF600 reader is activated and begins searching for the tag. Once the tag is identified, the truck is automatically weighed and its empty weight is displayed on an LED visible to the driver. Once a truck is successfully weighed, the driver receives a green light to drive forward and into the cement-loading silos.
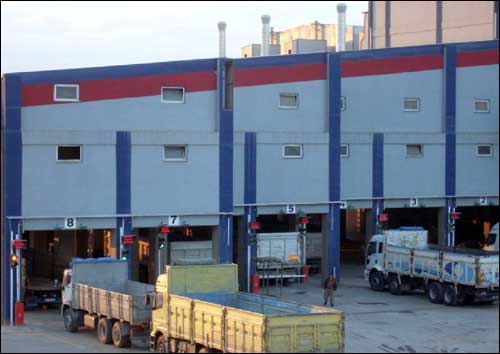
Once the truck has been identified at the scale, a series of large LED panels directs that vehicle to the proper loading bay, where it can accept either packaged or free-filling cement. Siemens RFID interrogators at the loading bays read the truck’s tag to determine whether the vehicle is authorized to enter the bay. If so, the system opens the barriers and the truck is allowed to drive in.
After loading is completed, the truck drives out and goes through another set of scales. The vehicle is again identified in the system via its RFID tag, to make sure it was loaded with the proper quantity of cement. The truck’s empty weight is compared with its loaded weight, which is crosschecked in the database with the amount that vehicle was authorized to load. If the amount is correct, the truck receives a green light and is allowed to leave the facility. While pulling out, the driver drops off the RFID tag.
“We’ve now improved the site’s capacity by 15 to 20 percent,” Tokat says. “The factory now operates at full capacity, 24/7.” In particular, he notes, the weighing process is now up to 10 times faster than before.
According to Tokat, implementing the system took just over three months from start to finish, with operations commencing on Jan. 10, 2009. It took the work of 10 Cimko employees and five Meyer RFID staff members to get the system operational.
The project cost €300,000 ($414,000). Not included in that sum are staff resources from Cimko’s IT department, which had to write much of the software to integrate the scales and the RFID system itself.
So far, Tokat says, he and his colleagues have been happy with the project’s performance. As the system has been running less than a year, he declines to provide a return on investment at this time, but says the project was important for Cimko “because it lets us use the factory more efficiently.”
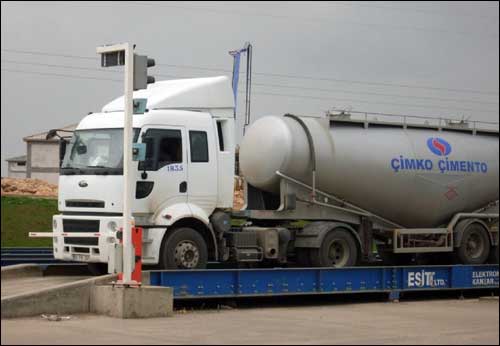
Meyer RFID’s Onur Bayindir estimates that Cimko saves as much as €100,000 ($138,000) annually using the system, because it eliminates the work of four full-time employees.
Other benefits cited by Tokat include the ability to replace various parts of the system for maintenance or repair extremely quickly—which is vital, given that the factory operates at full capacity. The new system also creates detailed reports for the company’s sales and finance units, enabling those divisions of the firm to have a greater level of detail and insight into its operations.
The company plans to roll out similar systems at its other concrete factories throughout Turkey, though a timeframe for widespread deployment is currently unavailable.