Griva, a textile manufacturer near Turin, Italy, has turned to RFID to address inefficiencies in its work-in-progress tracking system, according to Morgan Hill, Calif., RFID hardware provider Alien Technology. Within nine months of deploying a system consisting of Alien EPC Gen 2 tags and readers, Griva achieved a return on its RFID investment, says Ronny Haraldsvik, Alien’s vice president of marketing.
At its automated 1,000-square-meter factory, Griva produces approximately 300,000 rolls of fabric per year, much of it used to make flame-retardant curtains. At this facility, explains Stephen Crocker, director of channel management for Alien’s European market, raw materials are woven into fabric, which is cut and rolled around durable cardboard or plastic cores. Each role of fabric is then mechanically unrolled, treated and rerolled back onto the cores at 15 separate dye and coating stations in the facility, using a completely automated system. Each roll is identified and tracked at every step in the process, employing RFID hardware made by Alien and middleware provided by Simet, an Italian RFID systems integrator and middleware provider.
Under the previous system, Griva attached bar-coded labels to the end of each core prior to the start of the treatment process. Bar-code scanners mounted along the conveyor system transporting the cores from station to station would then read each label’s unique bar-code number. This would provide a work-in-progress manufacturing record, enabling Griva to track production. However, the high temperatures and industrial environment sometimes made the bar codes illegible. When a scanner failed to read a given bar code, a worker would need to manually interrogate and record the core’s ID number so the fabric could be traced.
Those bar codes remaining intact throughout the manufacturing process often become difficult to read once the rolls were covered in plastic film at the final production stage, because the film obscured the clear line of sight required for the interrogators to read the bar codes. In fact, Crocker says, the automated system could read only 70 percent of the stretch-wrapped rolls.
Now, instead of attaching a bar-code label onto each core, workers apply a label embedded with a passive EPC Gen 2 Alien Squiggle inlay. As each roll of fabric exits a treatment station, an Alien ALR-8800 interrogator reads the unique Electronic Product Code (EPC) encoded to its core’s tag. Simet’s RFID middleware removes duplicate reads and sends the tag ID number to Griva’s production-tracking application, which is part of its enterprise resource-planning platform.
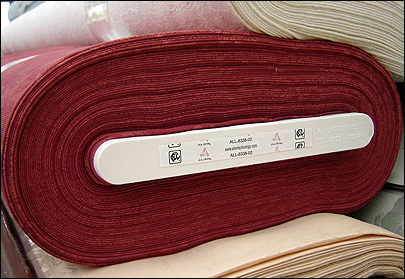
Griva could have deployed this manufacturing tracking system with high-frequency tags and readers instead of the ultrahigh-frequency EPC tags it chose, Crocker states, since the application does not require a long read range. However, the manufacturer hopes to eventually work with its trading partners to leverage the EPCs beyond the point of manufacturing, enabling the companies to track individual rolls throughout the supply chain.
Improving the reliability of its identification system led to lower labor costs. This also allowed Griva to keep its production lines operating at top speeds more often than it could under the bar-code system, which often required workers to stop or slow production to manually read or reapply bar-code labels to fabric roll cores. According to Haraldsvik, these factors led to Griva achieving a 30 percent return on its investment.
Griva’s application, Haraldsvik notes, is indicative of a growing number of RFID deployments that use EPC technology but are not driven by retailer or government mandates. “We’re seeing a lot of closed-loop solutions,” he says. “EPC is really starting to move out of the mandate world.”