All those sensors on automated guided vehicles (AGVs) which prevent collisions (with people, equipment or building structures) are constantly collecting data. Until recently, AGV manufacturers have been challenged to find a way to concretize this data and make it actionable, predictive and fundamentally useful.
This is a frequent complaint of Industry 4.0, big data, and the Industrial Internet of Things (IIoT): too much data, little of which can be accessed and used effectively. From tuggers, automated guided carts (AGCs) and AGVs, there is a real need to include IIoT monitoring. Asset management, asset tracking, predictive maintenance, remote monitoring of assets or conditions, and optimization are at the heart of IIoT initiatives.
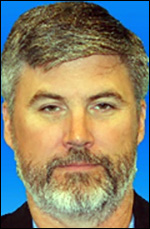
IIoT Drives Operational Efficiency and Improved OEE
The inclusion of IIoT monitoring ensures increases in operational efficiency. Eliminating the ripple effect caused by stopped vehicles is a metric of overall equipment effectiveness (OEE). The widely utilize data point, OEE, evaluates how effectively a manufacturing operation is utilized. The results are best used to identify scope for process performance improvement, and how to achieve the improvement. When the cycle time is reduced, the OEE will increase (more product is produced for less resource). More changeovers (setups) will lower the OEE, and this includes down-time from tuggers and AGVs not operating during production times. OEE measurement is used as a key performance indicator (KPI) in conjunction with lean-manufacturing efforts to provide a quantifiable measurement of success.
A single vehicle stopped in a high-traffic area has the potential to block all vehicles behind it. This means that a 15-minute stoppage for a single vehicle could mean 150 minutes of move time if there are 10 vehicles in the system. With an average move time of six minutes, that equals 25 moves within a 15-minute period—not to mention that many systems are not sized to catch up after a system error of that magnitude. Being able to utilize a remote management system allows for these types of errors to have an immediate corrective action implemented, and for the product to continue moving in a smooth and efficient manner.
IIoT Impacting Throughput in Manufacturing and Distribution
Without IIoT monitoring, plant managers, operations managers and logistics coordinators throughout manufacturing and distribution sectors lack the necessary real-time data for continuous vehicle status and health information.
An example of how an IIOT asset-management system works is at Vecna Robotics; a live and continuous flow of information is being sent directly to a highly skilled team of support engineers. In the event of an issue, corrective actions can be executed and/or recommended through remote asset engagement before downtime occurs. This translates to bottom-line throughput improvement.
Manufacturing throughput time is the amount of time required for a product to pass through a manufacturing process, thereby being converted from raw materials into finished goods. The concept also applies to the processing of raw materials into a component or sub-assembly. One important distinction of throughput at distribution centers is that a warehouse is typically used to store goods for longer periods of time, while distribution centers concentrate on faster turnover (or throughput) of goods.
IIoT Data Directly Impacts Safety
OSHA statistics indicate that there are roughly 85 forklift fatalities and 34,900 serious injuries each year, with 42 percent of the forklift fatalities resulting from an operator being crushed by a tipping vehicle. The Industrial Truck Association reports that the average life of a forklift is nine years, and there is a 90 percent chance of a serious accident during the course of its life. Seventy to 80 percent of the accidents impact pedestrians around a truck. Going fork-free immediately changes these dire and dangerous prognoses. Plants that implement zones fully or partially free of fork trucks realize significantly improved safety data, lower insurance rates and fewer workers’ compensation claims.
In the world of 24-7 monitoring, live video feeds from cameras mounted onto facility equipment are proving to be quite powerful in efforts to immediately address situations that may not be safe. Combined with sensor-level information, live video feeds offer another layer of visibility and data that companies can leverage, especially when it comes to ensuring full-scale operational safety, as well as security.
While there is absolutely a return on investment (IoT) calculation in IIoT monitoring services, one qualifiable data point is peace of mind. Knowing that the operation AGVs and their interaction with the plant floor is monitored non-stop by factory engineers represents a breakthrough in utilizing data to produce the safest and most efficient operation.
IIoT and Vehicle Maintenance
Maintenance is not a sexy topic when it comes to AGVs or tuggers. Few AGV vendors want to discuss the costs associated with maintenance, yet it cannot be ignored or neglected. Maintenance issues often occur with competing systems rendering the vehicle inoperable; plant floor managers then must notify a maintenance person to address the issue, locate the vehicle within the facility, travel to the vehicle, and then assess and address the issue.
This additional cost, combined with downtime, is rarely factored into vendor calculations and user ROI calculations. Omitting this cost is naïve at best and irresponsible at worst. For this reason, asset-monitoring tools and remote management capabilities in this new IIoT paradigm offer significant value to companies by reducing maintenance labor costs associated with nuisance error.
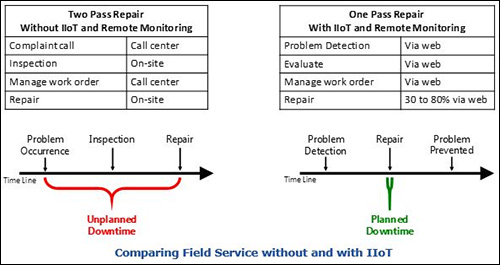
IIoT from a Different Perspective
The importance of the IIoT in logistics and manufacturing production is quite different from a lean-manufacturing perspective. In conducting an in-depth root-cause analysis, engineers determined the best approach to building a flexible and cost-effective IIoT monitoring solution. Free from being saddled with a commitment to a specific technology solution, this Six Sigma approach paved the way for authentic value stream mapping (VSM). This agile approach, coupled with a non-stop IIoT data stream, ensures that the future state of customers can be modified and adapted to needs as they arise.
This different view (one of robotics, not forklifts) has driven the use of a sensor suite, rather than an individual guidance type. This means that many different sensors can be used to achieve the best and lowest-cost solution to the customer. The sensor suite allows for the system to be used in a manner that takes the best of higher-costing AGV-type systems and lower-cost cart-type systems.
A sensor-based IIoT approach helps to ensure the new solution is flexible and capable of complex systems (such as with higher-costing legacy AGV solutions), as well as cost-effective (such as with low-cost cart-type systems). The recent introduction of real-time, high-level, non-stop asset-monitoring technology defines materials handling as a gamechanger. This approach positions AGVs with software that communicates with vehicles for traffic control, order generation, and routing locally and remotely.
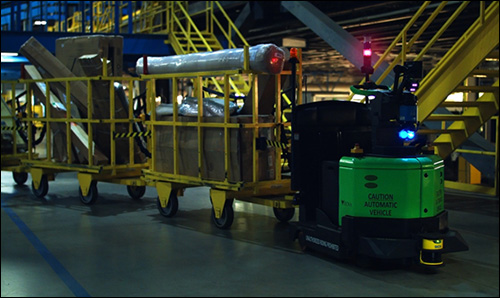
Part of the data transferred from the vehicle is local vehicle status information with respect to system anomalies. This data is also transferred directly to clients for immediate action, providing the maintenance and support team with the ability to fix issues and keep efficiencies high.
The most significant advancement is that local maintenance or support persons will never see these issues; with the use of the IIoT and the data transferred directly to the service facility, issues are assessed and addressed before they become visible to an end user. This nearly eliminates all user error handling and leaves these potential issues in the hands of the manufacturer.
John Hayes, Vecna Robotics‘ VP of sales and logistics, is a widely respected thought leader for the manufacturing, distribution and materials-handling industries. For more than 20 years, Hayes has been evaluating, designing, developing and implementing innovative software and hardware solutions, with a focus in the AGV space. He is a Supply & Demand Chain Executive “Pros to Know” recipient. Contact John at [email protected] or follow him on Twitter (@VecnaLogistics).