Florida Hospital‘s Celebration Health, established in 1997 in the Disney-planned community of Celebration, Fla., was an early adopter of radio frequency identification technology. Florida Hospital “has used RFID in one form or another since around 2005,” says Ashley Simmons, director of innovation development for Florida Hospital, which is part of the Adventist Health System. “In the early years, we relied on it for asset tracking and temperature monitoring, but we are now looking to use it far more extensively. There are huge opportunities to understand the flow of people and equipment—and bring greater insight and visibility to the business.”
Celebration Health, which performs nearly 10,000 surgeries annually, turned to RFID to rethink, remap and reinvent the fundamental way it delivers surgical services. “Providing an excellent patient experience has become a priority for hospitals,” Simmons says. “Hospital managers needed to know why a procedure was delayed, not just that a problem occurred, in order to take action to improve processes and patient care.”
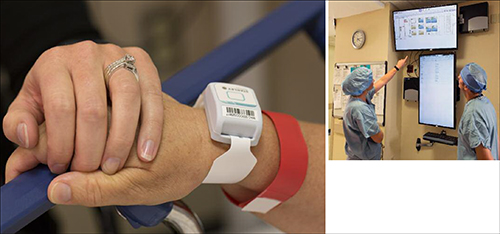
That meant using RFID to get answers to complex questions: What’s the root cause of bottlenecks that prevent on-time surgeries? How can we optimize room utilization? What information is required for effective in-the-moment decisions? How can we enhance the patient and family experience? To that end, Florida Hospital partnered with Stanley Healthcare to deploy an RFID real-time location system (RTLS) and build a platform with dashboards for analyzing real-time and historical data.
In 2015, the RFID initiative—now called the OR Patient Flow solution—was implemented in Celebration Health’s pre-op bays, 11 operating-room and two endoscopy suites, the 14-bed post-anesthesia care (PACU) unit, 31 patient rooms in the acute-care unit and the surgical waiting room. The hospital has real-time visibility into the location of patients, nurses, equipment and other assets. The data is used to enhance patient flow, improve communications and expedite room turnover. A dashboard in the waiting room displays the status of patients for family members and friends. Moreover, by plugging the data into analytics tools, “we are able to put the data to work to manage space and resources in a very efficient manner,” Simmons says.
Rethinking Care
Florida Hospital launched a broad RFID initiative in 2010. “At that time, we began building a new patient facility on the Celebration Health campus, and we wanted to make it a living laboratory for innovation,” Simmons says. Florida Hospital introduced a Center for Innovative Patient Care and formed a crossfunctional team, including representatives from administration, IT, nursing and surgical services, to oversee IT development and identify opportunities to put RFID and other technologies to work.
Once the team members began exploring how to collect, manage and use data to improve workflows, they quickly realized that real-time information generated automatically with an RFID RTLS solution was essential to the project. The hospital brought in Stanley Healthcare, which acquired AeroScout, to serve as the team’s implementation partner.
“We didn’t want to follow people around and create a Hawthorne effect, in which people know they are being studied and they change their behavior,” Simmons says. “We wanted to have an accurate understanding of what they really do. What’s more, instead of the data reporting taking days or weeks, the facility wanted to move to a platform that would tap real-time location services.” This would allow the facility to optimize scheduling and understand events on a minute-by-minute basis by studying the routes and movements of doctors, nurses and other health-care workers as they go about their daily tasks. “We could see how, by taking a different approach, we could reduce waste and increase collaboration among the teams,” Simmons explains.
RFID-tracking health-care workers provided valuable insights into their workflows, so the team decided to use the solution to better understand the dynamics of patient flow and how that, too, might be made more efficient. Most patients on the unit where staff workflows were being studied were recovering from surgery, so the natural progression was to monitor the location of surgical patients from registration through OR, recovery and discharge from the unit. The team members collaborated with hospital workers to identify the specific information required to visualize a patient’s full experience. Then, they established key performance indicators (KPIs), including on-time case starts, recovery times and efficiency of room turnover. To assess performance and adjust workflows to meet KPIs, they developed real-time and historical dashboards.
Remapping Processes
In 2011, Florida Hospital began building the current IT framework, including new servers, storage, and cabling to ensure sufficient Wi-Fi coverage to gather accurate location data. The hospital leveraged the existing Cisco Wi-Fi network and RFID-tagged assets, to track infusion pumps, beds and other mobile equipment. AeroScout tags with temperature probes were installed on pharmaceutical refrigerators and freezers, to continuously monitor the units and ensure they operated properly.
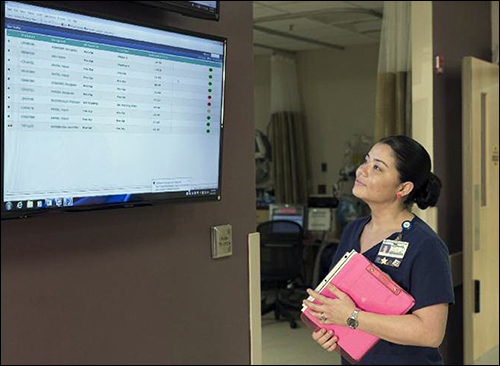
In 2013, the hospital began constructing the updated RTLS platform for managing surgical services. Stanley Healthcare engineers worked closely with Florida Hospital’s IT staff to configure and deploy the RFID system. Over an 18-month period, the team perfected the infrastructure to achieve high data accuracy and developed the real-time data visualizations and retrospective analytics dashboards that are central to the solution. “A real-time clinical application requires high data accuracy,” Simmons says, “and we met a realistic goal of 80 percent to 90 percent accuracy, always shooting for 95-plus percent.”
To achieve room-level accuracy to support the OR Patient Flow solution, AeroScout ultrasound exciters were added to the patient rooms in the surgical unit. More than 30 AeroScout low-frequency exciters were installed at several locations on the surgical-service department—including key entry and exit points in pre-op and PACU. In addition, 13 exciters were installed above operating tables in the OR and endoscopy suites.
Nurses and some physicians wear AeroScout tags attached to their employee ID badges, and patients wear the same tags attached with wristbands. When a tag “hears” an exciter, the tag reports the exciter’s unique ID number, which identifies a specific room, to an AeroScout MobileView server. The tag transmits data every 30 to 60 seconds (the facility uses a high beacon rate to enable precise tracking, even at the expense of battery life), using Wi-Fi access points on a Cisco wireless network. Data flows into custom-built software and an SQL database. Analysts use Excel spreadsheets, SAS analytics software and Stanley Healthcare’s MobileView Analytics, based on the Tableau platform, to examine the data and put it to work.
Because the system captures the location in real time, it is able to accurately time-stamp procedure start times, “wheels-in, wheels-out” events and room-status changes, important metrics to drive process improvement and better patient throughput. The infrastructure also enables other workflow applications, including the ability to automatically display a staff member’s identification when he or she enters a patient room, promote safety, and automatically document the amount of time a caregiver spends in a patient room.
“Once you move beyond tracking pumps or refrigerators with RFID, it gets a lot more complicated,” Simmons says. “There was a need to factor in Wi-Fi, ultrasound and other systems. R&D would test the systems in the lab but then, in the real world of the hospital, things wouldn’t always work the same way.
“We had to change the strength of the signal of the exciters and the tags,” Simmons adds. “If, for example, they were in power-save mode, some of them would not work correctly. We had to test multiple settings and different combinations to understand how everything worked together. We also had to tweak the Wi-Fi so that only certain exciters could actually trigger an event based on a previous exciter. It was just multiple trial and failure over and over until we figured out the right mix of settings.”
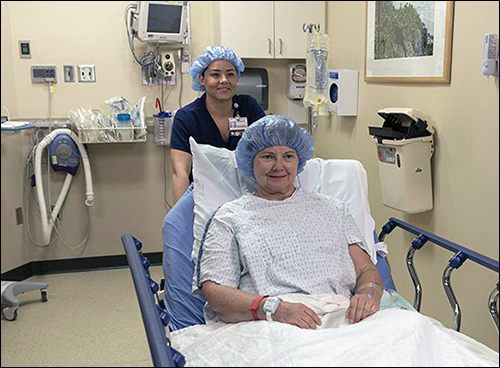
It was critical to not only deploy RFID to capture the data but also build logic into the platform, Simmons explains. “In many cases, multiple process flows can take place,” she says. “A patient, for example, may arrive at the hospital for a procedure, spend a few hours in recovery but then have another procedure scheduled later the same day.” Similarly, a nurse might take a patient to a specific room via a different route from one day to the next. “We had to have flexibility to identify when a change takes place—such as a canceled procedure or when a patient goes home,” Simmons says. “Otherwise, it could throw off the entire sequence of events and impact utilization of the dashboards due to decreased accuracy of information.”
The Florida Hospital-Stanley Healthcare team built the OR real-time map, list and dashboard views from scratch, to monitor all surgical services areas. The dashboard transforms the data into visual information so hospital staff members can see movements in real time, to better understand and adjust workflows for optimal efficiency and productivity. The visual dashboards allow staff members to look “upstream and downstream” to proactively manage patient throughput and staff scheduling, rather than simply react to events. It also enables staff members to see and respond immediately to potential delays or when the facility is approaching a high-risk level.
“At a high level, processes in an OR seem highly standardized,” Simmons says. “Once you gain finer-grained visibility into movements, randomness begins to emerge. Even within a strict protocol, there is still room for considerable variation in human behavior.”
Reinventing Services
The OR Patient Flow solution is helping Florida Hospital to meet its goals to improve surgical services performance and, thus, the patient experience. The historical dashboards enable managers to review a day’s performance, see failure points and drive continuous improvement.
The real-time pre-op dashboard includes a list of patients checked in and waiting or in pre-op. “The staff can actually see that a patient has checked in—that he or she is in the waiting room or in pre-op, so the surgical team can start preparing,” Simmons says. “They can see whether the necessary equipment and staff are available. If there’s a delay in case start due to patient arrival or other variable, for example, the team can proactively manage the schedule to continue progress of other patients through the process. All of this keeps the day moving and helps the staff be efficient with our resources and timely for all of our patients.” This visibility supports the goal of on-time first case start, which can impact the on-time starts of subsequent procedures throughout the day.
“Overall, the hospital has achieved a 10- to 24-minute reduction in total time in recovery for OR patients,” Simmons says. The sooner patients are released (once they have met care criteria), the faster they are reunited with their families, whether they are discharged to go home or transferred to the acute-care unit. What’s more, she notes, “total recovery times are far more predictable, with an average of 20 percent less variation.”
The real-time PACU dashboard includes a list of patients in surgery or recovery, so caregivers know when to expect them. Staff members can also see the status of rooms in the acute-care unit, so they can understand any delays in moving patients there. The PACU has achieved a reduction of six minutes to 16 minutes in hold times. Similarly, the real-time acute-care dashboard lets caregivers know when to expect patients from the PACU. The dashboards have led to a 75 percent reduction in phone calls and person-to-person communications between staff members to confirm basic information.
The OR Patient Flow solution has also improved the room-turnover process. When a surgical patient leaves an OR or endoscopy suite, the system automatically changes the room status to “soiled” and the icon for the room on the map changes color to brown. When environmental services is finished cleaning the suite, a worker pushes a button on an RTLS tag at the exit to change the room status to “available,” indicated by green. The event information is time-stamped and logged into the system. This data can be analyzed with the room-utilization dashboards to identify bottlenecks and investigate why rooms are sitting idle.
The dashboard in the surgical waiting room “provides families and friends with the current status of patients,” Simmons says. “People know immediately what is taking place and where their loved one is located at any given moment.”
Celebration Health plans to expand the RFID solution to the emergency department. As Florida Hospital perfects the RFID systems, they’re made available to other hospitals in the Adventist Health System.
“The current solution represents the early stages of technology innovation and transformation,” Simmons says. Florida Hospital is continuing to develop and perfect dashboards and analytics tools. “For a number of years, RFID was used in a very basic way,” she says. “We have gotten to the point at which the technology works extremely well. We are seeing huge value in building out a platform based on RFID and RTLS and seeding the technology to the entire company.
“This project has opened our eyes to a whole new level of data, information and knowledge,” Simmons adds. “There are new use cases emerging and they will continue to shape the future of health care.”