While most energy in France is supplied by nuclear energy facilities, at times of high load, utility company Électricité de France (EDF) relies on natural gas to meet those increased demands. When those (usually dormant) natural gas turbines are powered up to supply additional energy, it is critical that they function properly. The EDF’s Centre d’Exploitation des Turbines à Combustion (CETAC)—Combustion Turbines Operating Center—is responsible for maintaining those turbines. To meet that mandate, the organization operates 13 production units at seven sites and stores spare parts at eight storage areas.
Recently, CETAC began employing RFID to ensure that if any piece requires replacement or repair, the necessary spare parts can be located within the shortest possible span of time. The technology, provided by Nexess, includes EPC Gen 2 passive ultrahigh-frequency (UHF) RFID tags from Omni-ID. Four months ago, says Olivier Roualt, Nexess’ product manager, CETAC installed the technology at its Champagne-sur-Oise and Brennilis sites.
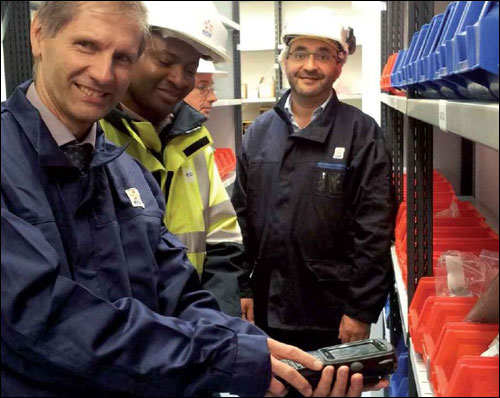
Typically, CETAC reports, if the energy company switches on a gas turbine in response to spikes in demand for electricity, the system functions fine. However, because the turbine has remained dormant for some time, it is possible that a part may fail, in which case the problem must be quickly diagnosed and the replacement part identified and installed. Traditionally, if such a process is required, personnel must view Microsoft Excel spreadsheets in order to determine where replacement parts are located, make phone calls and, in some cases, walk to the storage area to visually seek a particular item. CETAC wanted to be sure it knew each spare part’s exact location at all times.
The solution chosen needed to be easy to use and enable goods’ locations to be ascertained without the need for eye contact, says Claude Veau, CETAC’s technical director. Removing the need to visually check every item and serial number printed on it would make the process of locating a replacement part considerably faster, the company explains. In addition, however, CETAC wanted to reduce the amount of data-entry time required for an employee using an Excel file to input the latest location of a part any time it was moved.
CETAC has tagged 5,000 items to date, with a goal of tagging as many as 70,000 items across all of its sites. First, the Omni-ID on-metal Prox-NG tag, made with an Alien Technology Higgs 3 RFID chip, is attached to the item via an adhesive. The tag’s unique ID number, along with details about the part to which it is attached—such as its lot number, serial number and manufacturer—is then stored in Nexess’ NexCap Mobile Asset Tracking software, residing on CETAC’s server. When the item is put away, a staff member uses a Motorola Solutions Psion Workabout Pro 3 PDA with a built-in UHF RFID reader to interrogate the tag. He or she then inputs the building and shelf number where the part is being stored, and this information is forwarded to the NexCap software via a Wi-Fi or cable connection.
In the event that a part is needed, workers access the NexCap software on a PC, or in the handheld’s firmware, and enter the part number or description. The software then provides the locations of any items fitting that description or part number. Personnel can also carry the handheld while visiting that storage location, and use its Geiger counter functionality to identify the proper part. When the tag is read—within a distance of about 1 meter (3.3 feet)—the PDA displays the component’s description. The worker then indicates that the item is being removed, by responding to prompts, in order to update the part’s status.
In addition to tagging all items at all seven sites, CETAC hopes to have the NEXCAP software integrated with its own inventory-management software on its nationwide server. This will allow the staff to locate all items at any of the multiple sites.
Because the technology provides location data, CETAC’s workers no longer need to conduct inventory checks at each of its storage locations on a regular basis, thereby saving the company money in terms of labor costs. What’s more, the firm does not need to order excess stock that would otherwise be purchased if a specific item could not be found. Veau predicts that CETAC will see a return on its investment within less than two years, based on these benefits.
“The solution works perfectly,” Veau reports. “In fact, it was needed to find a spare part in an emergency, due to a turbine failure.” Staff members simply input the required part into the handheld reader, he says, adding, “The PDA located the spare part right away and gave us the location.”