I was recently thinking about the unique mindset of those who have come before us and have laid the groundwork for our continued advancement. I read an article explaining the history of North America and somehow found myself making a connection between the explorers of the past and the innovators of today. What do explorers from the 15th and 16th centuries and an innovative RFID company from the 21st century have in common? It most certainly is not their clothes or their mode of transportation. It is not the technology that is or was available to them. The commonality lies in the way they think.
On the surface, it may be tough to correlate the similarities, but when you peel back a layer or two, there is a similar mindset that clearly begins to show. A mindset of finding a new way at all costs. A mindset that desires to do something no one has done before. A mindset of never giving up and pushing the limits at all costs. A mindset of needing team members willing to explore or innovate with you. The mindset of leveraging the unique strengths of each member of the team.
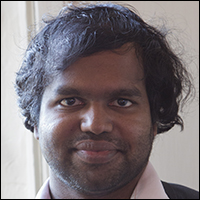
Sabesan Sithamparanathan
When you look at it this way, it is not that hard to understand there just may be similarities although centuries apart. Any good innovation or exploration starts with a goal. It starts with something you are trying to achieve. Or maybe it is something that has been achieved, yet an innovator or explorer strives to achieve it differently, to drive a different result, or to increase efficiency. There is no more obvious time to see this than in our world today.
The recent COVID-19 pandemic brought to the world’s stage the medical and pharmaceutical industries’ attempts to rapidly innovate and improve vaccination efficacy. The world watched as Pfizer, Moderna, AstraZeneca and others took different paths of innovation in the attempt to create a vaccination that has the highest percentage of effectiveness. This is the innovation mindset, and as I thought about the world in the 15th and 16th centuries, this was the mindset of explorers of the past: to go somewhere no one has ever been, do it in the most efficient way and take as little risk as possible.
Our RFID commercialization team set out on a path of innovation—or should I say exploration. At times, it feels like both. With my time at Cambridge University focused on RFID innovation, it became obvious that to get passive (battery-free) RFID to be accepted and effective in more use cases, we needed to solve an inherent challenge we encountered with conventional RFID reader technology. Accuracy was the most obvious challenge associated with passive RFID technology. After all, passive RFID was developed, in most use cases, to eliminate steps or human intervention and still capture data necessary to accurately track or monitor.
We knew this is where passive RFID technology was falling short, and my colleagues and I began to look at how we could explore different ways to solve this accuracy challenge. Knowing this high-level challenge, we continued to seek knowledge about the use cases for which RFID was being utilized. We learned there are some use cases for which a high level of accuracy is desired but not critical, and that there are other use cases in which it is absolutely critical. It became very important for us to learn as much as possible about these different use cases, especially around those that have a critical need for accuracy.
For this reason, we discovered a system designed to monitor foreign object debris (FOD) in aerospace manufacturing and maintenance operations. This unique solution was developed to tackle the challenge of tool accountability around critical jobs. Few jobs are more critical than building or fixing airplanes. What a costly mistake it can be to leave a screwdriver, ratchet or any hand tool in a jet engine or fuselage. Not only can it be a large financial cost, but it can also be a life-threatening risk to the pilots who test-fly these planes. It has been a great concern for aerospace manufacturers of all sizes and a challenging process that requires many checks and balances.
It is estimated that FOD costs the aviation industry $13 billion per year in direct and indirect costs, including flight delays, plane changes and fuel inefficiencies. To help solve these challenges and reduce risk, an RFID toolbox was specifically designed to manage tool inventory in operations in which FOD was a great concern. Manufacturers like Boeing, Lockheed Martin and Airbus have adopted such solutions to reduce risk and improve efficiency.
The concept is simple. In an environment in which FOD is critical, there is no room for error. If a tool is used to assemble an aircraft, that tool needs to be accounted for at every transition point of the process. Every change of shift and every assembly job change needs a process in place to make sure no tool has been left inside the plane during assembly. That seems obvious, yet it happens far more often than you would imagine. So, these toolboxes enable a digital confirmation that every tool was back in its place and signed off on by multiple workers before they moved to the next step.
Due to some of the inherent challenges associated with passive tags on durable items, as well as the limitations of conventional readers, there was a need for a breakthrough. Conventional readers were creating a few immediate challenges, chief among them the accuracy of reading the tags. Although there was an effective signal trap inside the toolbox, there were still challenges with reaching the 99%-plus tag reads in the necessary time required for an effective FOD solution. Some great software features were written to ensure positive control, but if we were able to increase the percentage of accurate tag reads, we’d thus reduce the time to levels necessary for practical use.
Secondly, because of the challenges inherent in accurately reading tags, there was a limitation on the number of tools a cabinet could contain. This was not a space or capacity issue—it was a tag blind spot issue. Thirdly, the time it takes to detect tools inside the cabinets was important. The issue was related to how long it took for a conventional reader to recognize the tag. Although the reader might eventually read the tag, it became a practical timing and confidence issue as a mechanic would wait to receive the “all-in” notification. Ultimately, these issues were limiting the number of tagged tools that could be stored in the cabinet, and hence the practical viability of the product.
By working closely with the toolbox manufacturer and implementing enhanced reader technology that provided the 99%-plus accuracy, range and speed necessary for these safety-critical applications in sufficiently short time for commercial use, we were confident we could enable the toolboxes to securely store the required number tools in each cabinet. It seemed like a perfect time for exploration.
Rolling up our sleeves and getting to work, we were able to make improvements in all three areas (accuracy, speed and volume). Because of the unique signal-processing methods with which our team from Cambridge designed the readers and the way we were able to interpret tag reads, we were able to improve the read accuracy to 99%-plus in a use case for which it is the most critical aspect of the solution. We were also able to increase the number of tools a cabinet could store and accurately read by 200 percent. This enabled us to reduce the overall cabinet footprint on the assembly floor and improve efficiency by reducing transaction times by 50 percent or more, in some cases.
We have been very impressed with the improvements, but most importantly, the aerospace customers have been impressed. That is what really matters, whether the end users align and extract immediate value from their investment. When tools are returned to the cabinet now, customers get 99%-plus reads within eight seconds. That was something that just wasn’t happening with conventional readers. We were very happy to help a solution get to the next level. The results confirm that we achieved our goals, and we are proud of those accomplishments.
One thing I have learned throughout the years is that sometimes the best results come with the best surprises. That is the case for this project. We recognized in this use case that tag degradation was common. When a passive tag is applied to a durable item for a lengthy period of time, we would see it weaken as it aged. In a use case like the RFID toolboxes, this becomes critical because of the need for a high level of tag accuracy. When tracking consumables with disposable tags, that is not necessarily the case, so we had to find a way to make an old tag still read like a new tag—a great challenge which we were able to overcome. So now, we can ensure that there remains a high level of read accuracy with tags of all ages, sizes and designs. We were able to accomplish this and provide significant user benefits, confidence and accuracy.
That leads me back to the likeness of an innovator of the 21st century and an explorer of the 16th century. It leads me back to mindset—the mindset of discovery. The desire to be the first. The desire to be able to provide benefits to many. Whether that is by stepping out on the deck of a 16th-century schooner heading off to unknown territories or developing technology to read radio frequency signals. In 1513, Spanish governor Ponce de León set sail in search of a fountain or spring rumored to retain the youth of anyone who drank it. In the process, he discovered La Florida and later returned in 1521 to establish the first Spanish colony in the new land.
In 2019, we set on a journey to make old radio frequency tags read like they were young again and, in the process, discovered a solution to improve the livelihood of aircraft assembly technicians and reduce their risk. See the similarities? I guess we will never stop striving to make old young again. Never stop enabling us to perform at our highest level at a time when we are most wise. Never stop exploring, innovating and searching for something new. Whether you are innovating or exploring, aim for the sky and never stop believing, because every little step leads you closer to your destination. It is up to you to determine where you are heading and simply take the first step.
Dr. Sabesan Sithamparanathan is a multi-award-winning entrepreneur with more than 15 years’ experience in the IoT space. Sabesan founded PervasID based on his Ph.D. research at Cambridge University. He invented and developed the world’s most accurate passive RFID technology. As founder and CEO, Sabesan successfully grew PervasID from its inception to a global enterprise, providing transformative solutions to the healthcare, industrial and retail sectors with a complete product suite. Throughout his career, he has been an expert in entrepreneurship, strategic business development and innovation leadership. Sabesan was awarded a Queen’s Award for Enterprise in Innovation and the Royal Academy of Engineering’s Silver Medal.