Aug 03, 2015San Diego's Scripps Memorial Hospital Encinitas has adopted MEPS Real-Time's Virtual Logbook, in conjunction with MEPS' Intelliguard Kit and Tray Management System, to record when medication-filled trays leave the hospital's pharmacy, where they are going and when they are returned to the pharmacy. Virtual Logbook enables the hospital staff to easily input the location where a tray will be going, thereby saving employees time spent seeking RFID-tagged medications on those trays when they are required elsewhere, or if any are recalled or nearing their expiration dates.
Scripps Memorial Hospital Encinitas has 192 inpatient beds and performs 4,800 surgeries annually. The medical facility has been using the Intelliguard Kit and Tray Management System for a year and a half, and has achieved a reduction in labor, as well as in errors related to the packing of medicines on each tray. Trays for use with pharmaceuticals for neonatal, pediatric and adult surgeries, as well as anesthesia, are sent to the operating rooms to ensure that the medications are available as needed for each surgical patient. Other trays are delivered to locations throughout the hospital where patients are treated.
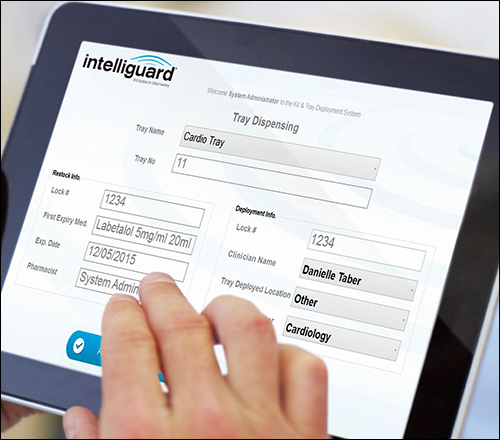
Before installing the Intelliguard Kit and Tray Management System in November 2013, Scripps Memorial employed a manual method for identifying which medications were on which tray, as well as the expiration date for each drug. To ensure that errors were never made, such as the wrong medicine being packed on a tray, or one that would soon expire, workers had to visually check and double-check every item, a process that took nine to 27 minutes per tray to complete. Each tray typically has 16 to 139 items packed on it, and the hospital has approximately 100 trays (there are 14 different tray types) in use on any given day. Altogether, the repacking of trays takes place 6,100 times each year.
Despite the careful checking and re-checking performed by pharmacists and technicians at the pharmacy, the process still left room for error. The hospital conducted an internal study and found that expired drugs could still find their way onto trays, and that trays were sometimes missing medications.
Such errors are a concern not only to hospitals, but also to health-care agencies, including the California State Department of Public Health and the California State Board of Pharmacy, says Doug Johnston, Scripps Memorial Hospital Encinitas' director of pharmacy. Hospitals typically receive unannounced visits from these agencies and others each year, with pharmaceutical inspectors looking to view medication trays, what's on them and when each drug is due to expire.
The Intelliguard workstation has a built-in Impinj or ThingMagic reader and an enclosed area for trays, explains Shariq Hussain, MEPS' CEO and president. Scripps uses such a workstation to encode ID numbers to ultrahigh-frequency (UHF) RFID tags made with Impinj Monza chips. Each tag is then attached to a medication, and the tag's unique ID number is linked to the drug's name, dosage, drug identification number (DIN) or National Drug Code (NDC) number, lot number and expiration date.
A pharmacy worker fills a tray with the RFID-tagged medications, places it the workstation's enclosed area and presses prompts on the touch screen to indicate the tray type, such as pediatric anesthesia. The workstation's RFID reader then captures the IDs of all the tags, and the Intelliguard Kit and Tray Management software verifies that the medicines are correct for that specific tray, and that none are expiring. (According to Hussain, MEPS custom-designed its workstation's reader antenna to ensure that all tags on a tray placed within the enclosed area can be read.) In the event of a problem, an alert is displayed on the workstation's computer screen. If the tray is packed correctly, the system stores that data and the tray can then be sent for use in the surgical unit or other areas of the hospital.
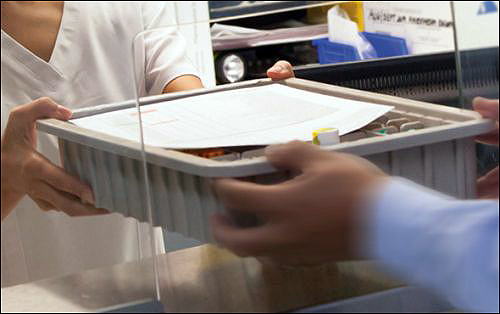
Once the hospital pharmacy had gotten used to the Intelliguard system, Johnston says, he requested an added function that would eliminate the need for a written logbook to be filled out by staff members when trays were taken from the pharmacy. With Virtual Logbook, a user who takes a tray to the appropriate location opens the Intelliguard software on a tablet and uses the device's touchscreen to enter the ID number printed on that tray and select its intended destination. Once a tray is returned to the pharmacy, a worker updates its status, thereby indicating that it has come back. In this way, pharmacy personnel can easily determine where a specific medication is located, which can prove helpful if any drugs on that tray have been recalled or are nearing their expiration dates.
When a tray has been returned to the pharmacy and needs to refilled, a worker places it back in the workstation. The Intelliguard system then reads the ID numbers of the tray's tags, compares them against that tray's assigned medicines and displays a list of all items are missing, expired, recalled or soon-to-expire. Employees then restock the tray accordingly with RFID-tagged medications from the pharmacy shelves.
The system does require some time be invested to tag medications. The time study conducted by the hospital found that it takes a technician approximately 14 seconds to tag and encode a single unit of medication, and a pharmacist approximately two seconds to double-check the accurate input of that drug unit. However, when it comes to the processing of trays, the Intelliguard Kit and Tray Management System saves 19.5 minutes, on average, for a large tray and 6.3 minutes for the smallest tray. These figures total about 1,500 hours of annual time savings from using the Intelliguard system for processing and approving trays.
When it comes to locating a tray in the event of a drug recall, a manual method requires staff members to open every single tray that includes that recalled medication in order to check whether that specific lot number is on the recall list. This process can take days to complete. In the past, Johnston says, if he knew that an inspection was imminent, he sent about seven workers out into the hospital to go over every tray and ensure that no medicines were set to expire. This project, he adds, could take the group an entire night. With Intelliguard, he can accomplish the same task alone in around 10 minutes.
Johnston says he doesn't tend to find any problems, since the solution is designed to catch approaching expirations as they occur.
"When you see the number of trays the pharmacy has to go through in a single shift," Johnston states, "you can understand that [with a manual system], they're going to take short cuts. They may not look at dates," he adds, or carefully read the names of the medications. Even with a second set of eyes, he notes, shortcuts could be taken. The hospital's internal study found that performing the manual processing properly would require an additional 1,500 man-hours per year.
Since the MEPS Intelliguard system was taken live, Johnston reports, the hospital's staff has expressed satisfaction with the new technology. "They love the efficiency around this," he says.
With Virtual Logbook, Johnston says, the actual time savings of knowing where in the hospital a tray is located, based on data input by the staff, has not yet been measured. However, he notes, running a report in the Intelliguard software to pinpoint a drug's location, versus sending workers out to physically retrieve and search through carts and trays, "can be potentially very significant in terms of savings."
Another Scripps medical facility, Scripps Mercy Hospital, is now trialing the same technology, Johnston says. If that trial goes well, he adds, all five Scripps hospitals, as well as a centralized pharmacy at another location, will adopt the system.