Feb 05, 2021Blasting solutions company Davey Bickford Enaex, with help from French research center CEA-Leti, has developed a wireless two-way communications system to remotely control electronic detonators in mines. The solution leverages a proprietary active RF protocol that enables a blaster to communicate with thousands of detonators before triggering each explosive device. The system was demonstrated at a mining site in Chile in December 2019, and the company and laboratory signed a joint agreement for the wireless blasting system last December, with the plan of making the technology commercially available.
The solution was developed to eliminate the need for surface wiring at mining sites, and to wirelessly enable bidirectional control of multiple electronic detonators from a single, safe location, thereby making the blasting process less risky and more efficient. Integration of wireless technologies into its initiation systems has been at the core of the company's development roadmap, says Aymeric Denuelle, Davey Bickford's product marketing manager, "to always provide safer solutions that enable our customers to trigger larger blasts from a remote firing point."
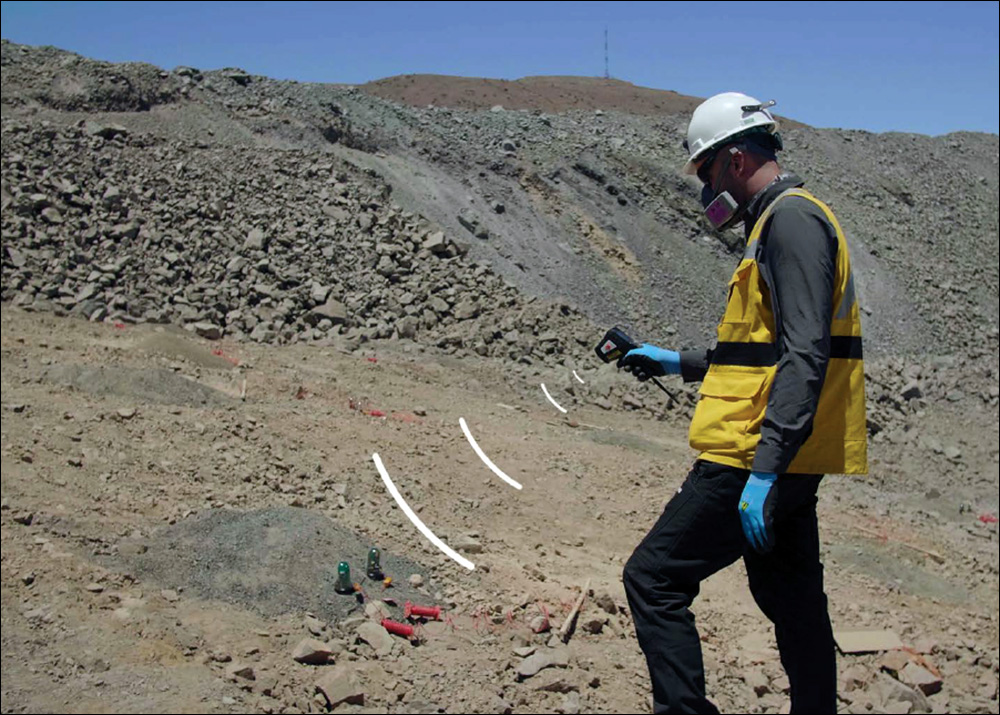
Mining personnel manually check conditions and ensure an environment's safety before blasting is initiated.
The system developed by the two entities consists of Davey Bickford's radio modules installed in electronic detonators, as well as a blast controller that sends directives to each unique detonator and requires the appropriate response from each device before initiating a blast. The solution has been found to transmit across several kilometers, enabling it to accommodate the relatively long distance between the digital blasting system and the actual blast site that typically exists at open pit mines.
Blasting operations have historically posed a hazard for mining environments. Mining company personnel would manually check conditions and ensure an environment's safety before blasting was initiated—a process known as "priming the blast." This can be costly in terms of labor hours, as well as risky in the event that a human error is made. What's more, the staff in charge of blasting must avoid misfires that might cause additional hazards after a blast, once the extraction of the resulting muck pile has begun. The main issue was related to the fact that the crews were unable to determine whether any detonators failed to go off.
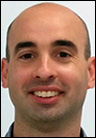
Aymeric Denuelle
During the late 1990s, some key suppliers of blasting products and services pioneered a new generation of detonators, with electronic components inside. The electronic chips enable the devices to communicate to the shot firers—forward and backward—until the final moment before the blast is triggered. The wires connecting all detonators to the blasting machines enabled that essential safety functionality, Denuelle says, "but was also one Achille's heel of the system, in terms of implementation complexity and network electric leakages."
Davey Bickford manufactures a variety of initiation systems for surface and underground mining, quarrying, construction and exploration applications. The company serves Europe, Asia, Australia, New Zealand, and North, South and Central Americas. When it met with CEA-Leti, the firm sought to develop a solution for its customers that would provide wireless two-way communication with the detonators before any blasts occurred. All detonators remain functional until the last moment, awaiting the "fire" order. The resultant solution is known as DaveyTronic Edge.
CEA-Leti, located in Grenoble, France, is a research institute focused on electronics and information technologies that provides applied research in microelectronics for wireless solutions (see Company Boosts Sensitivity and Shortens Length of Its RFID Yarn and French Handball Team Trains with Warable RFID Sensors). The laboratory first entered into conversations with Davey Bickford in 2014. "The main topic was to remove the wire between the control unit and the detonator," says Swan Gerome, CEA-Leti's business-development manager. While electronic detonators are not new, he notes, the wireless connectivity for timing is a recent innovation.
Back when the lab and technology company commenced development, Gerome recalls, there were few wireless systems available. Those that were in use were unidirectional—in other words, detonation signals could be sent to a detonator, but no response could be received. The company had two objectives with the new wireless system, according to Vincent Berg, the head of CEA-Leti's Smart Object Communication Laboratory. One was to make the detonation process more efficient, he says, noting that mines need to leverage their time primarily in mining, rather than the detonations.
"Time is money in this industry," Berg states. "They need to spend more time collecting the ore than to do the blasting." Bidirectionality was also central, he adds. "You need feedback about the state of the detonator." To properly control detonation, he says, "You need to time and coordinate the detonations very accurately so that the shockwave is synchronized." Development commenced in 2017.
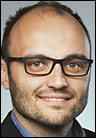
Swan Gerome
With the new system, the wireless detonator has a built-in cylindrical device that includes a LoRa radio and antenna utilizing the low-power wide-area network (LPWAN) protocol. The module can receive and accept a prompt to detonate within a specific amount of time, but before the detonation takes place, the state of the detonators needs to be monitored. If a detonator fails to respond properly, for instance, operators can cancel the blast and replace the non-working or unstable device. The unit in each battery-powered detonator has its own unique identification, and it sends and receives data at a distance of up to several kilometers between the detonator and the blast controller.
The controller has two modes, one for programming and the other for blasting. To set up a detonation, users access the programming mode to choose blasting parameters for each detonator. The unit then receives a response from each detonator, acknowledging its instructions. Once it is confirmed that every detonator has responded appropriately, users can switch to blasting mode to launch the explosion. The detonator is reduced to dust after the blasting, so no detonators should respond when they are queried after a blast has taken place. The solution leverages a proprietary protocol based on LoRa, Gerome says, and CEA-Leti designed the antenna to operate with the dedicated protocol to respond to specifications unique to the outdoor mining environment.
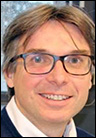
Vincent Berg
While developing the solution, Gerome reports, the research team considered numerous wireless network protocols but were limited by the mining industry's requirements. They needed a long-range option and wanted to focus on a bidirectional option. They also required that transmissions be sent fast, because when a lasting trigger is sent, it is vital that every detonator has the same time reference for when the blast was initiated. The blasting instruction data is all managed on the controller device and is not saved.
A successful demonstration of the system took place in December 2019 at the mining site in Chile's Antofagasta region, involving approximately 200 detonators. The entities then agreed to carry out further development to build a commercially available solution. The ongoing work will take place with assistance from IRT Nanoelec, a Grenoble-based consortium focused on R&D in semiconductor devices and communication technologies.
"This solution works toward humanizing mining and providing greater safety and efficiency to our customers," Denuelle says. The technology, he explains, decreases the operational burden for workers and ensures blasting takes place on time, and less often, while maintaining two-way communication and meeting safety standards. "Detonator deployment is facilitated by the removal of surface wires and contactless timing," while troubleshooting is made easier and blast size is no longer limited by such electrical considerations as the number of wires that would need to be run.
Images courtesy of Davey Bickford Enaex.