Aug 01, 2005More than 90 percent of international trade now involves shipping goods in sea-going vessels, including 95 percent of all goods bound for the United States, according to a study by the management consulting firm A.T. Kearney. But moving goods from factories to retail stores is becoming increasingly complex and that's leading to problems—problems radio frequency identification could help solve.
The logistics industry includes trucking, rail and shipping companies, which tend to transport bulk freight, and air cargo companies, which focus primarily in the express shipment market. But most manufacturers, rather than sort out the labyrinth of shipping lanes, ports, customs, trucking and air cargo issues, outsource the flow of goods and information management to logistics providers.
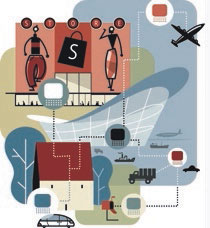
Third-party logistics providers—or 3PLs, as they are known—provide transportation and warehousing arrangements, and act as brokers between shipping and other transportation companies and customs officials along certain specified trade routes. Due to the increasing volume and complexity of global trade, and a rash of consolidation between some freight, trucking and air cargo companies, manufacturers are increasingly outsourcing the management of their entire supply chain to fourth-party logistics providers—4PLs—that have global reach and access to different modes of transportation.
A 2004 study by the consulting firm Capgemini found that 79 percent of North American companies outsourced to 3PLs; so did 76 percent of firms in Western Europe, 84 percent in Asia Pacific and 67 percent in Latin America. The companies said logistics providers help them gain strategic advantage in the marketplace by ensuring that their goods get transported to the right destination at the right time.
But manufacturers pay a price for this service: The data they receive about their products during shipment is often inadequate, and companies lose visibility of their products. When Capgemini surveyed these companies about what future IT-based logistics services they may need in their businesses, the overwhelming response—53 percent in North America, 61 percent in Western Europe, 59 percent in Asia Pacific and 48 percent in Latin America—was a need for RFID and asset tracking services.
A.T. Kearney recently surveyed supply chain executives from 183 companies that account for nearly one-third of the total goods shipped overseas to and from the United States, including players in the retail, consumer packaged goods, automotive, chemicals and high-tech industries. "One of the biggest complaints we got from 90 percent of the executives we interviewed was that the data that they get back is fairly untrustworthy and not sufficient to run a sophisticated supply chain," says Omar Hijazi, the principal analyst who authored the report. "There are so many intermediaries, ports, carriers and shipping companies, and a lot of it is done manually." The manual data sometimes contains typographical errors or arrives after the fact.
It's a situation that offers logistics companies a huge opportunity to provide value-added RFID services to their customers that promote efficiency and visibility. RFID could also help companies meet government initiatives to secure containers in the supply chain. But companies are experimenting with RFID only as far as their budgets will allow. The airlines have had to set back any timetables for introducing RFID in their air cargo operations due to widespread financial problems in the industry. Trucking, shipping and rail companies also run on thin margins in competitive fields but are experimenting with RFID.
The 3PLs and 4PLs may be in the best position to provide end-to-end RFID solutions along certain heavily traveled and lucrative transportation routes. The goal would be to capture quality data about cargo shipments and sell that information on a real-time basis to customers. But logistics providers are concerned that in this cutthroat business, customers will come to expect RFID services as a cost of doing business and won't be willing to pay extra to cover the expense of building an RFID infrastructure.
There's also competitiveness among logistics providers, and the industry faces huge technical challenges. (To learn how the logistics industry is solving these issues, see the box on the opposite page.)
A number of the bigger logistics providers—mostly 3PLs and 4PLs—already offer value-added RFID services. DHL developed a new line of business after the Metro Group, Germany's largest retailer, started requiring its top 100 suppliers to tag pallets and cases of goods as of November 2004. To its line of express mail, parcel and worldwide logistics solutions, the Bonn-based DHL introduced its "TAG-Fit" service. For a fee, DHL sorts out cases and pallets of its customers' goods destined for Metro. Then it encodes RFID tags, converts them to labels and applies the labels by hand to the right shipments. DHL tests the readability of the tags before transporting the goods to Metro's distribution centers.
In selling the service to customers, DHL argued that by outsourcing RFID tagging to a third party, manufacturers could react more quickly to retailer mandates, reduce the cost of tagging by requiring no up-front investment and better keep abreast of new technologies. It was an offer some manufacturers couldn't refuse. DHL now has 20 customers who pay for RFID tagging, and more business may be on the horizon as Metro expands its RFID mandate to cover its top 300 suppliers on Jan. 1, 2006.
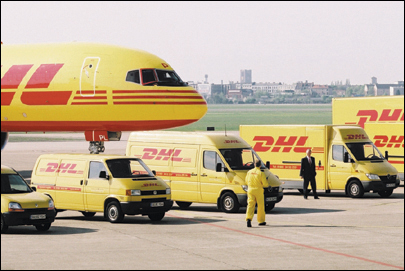
APL Logistics, a unit of Singapore's $6.5 billion shipping and logistics giant Neptune Orient Lines, provides end-to-end logistics services for a variety of customers around the world. In February, APL Logistics joined with its parent NOL to open the RFID Testing and Solutions Center in Singapore, one of Southeast Asia's first such laboratories. The center simulates the receiving environment at retail distribution centers of several companies that have mandated their suppliers to start tagging shipments, including Metro and Tesco in Europe, and Wal-Mart, Target and Best Buy in the United States. Manufacturers can have their products tagged and tested to see how well the tags are read as pallets and cases move through dock doors on conveyor belts.
Exel, an $11 billion worldwide logistics provider based in the United Kingdom, has seen up to 25 percent of its U.S. customers either evaluate or deploy RFID as a result of retailer or U.S. Department of Defense mandates. Tony Hollis, Exel's manager of RFID strategy and execution, says the company has assisted many consumer packaged goods companies with these initiatives by applying RFID tags, setting up infrastructure and helping set up pilots. But Hollis—like other logistics providers interviewed—believes that the slap-and-ship business will not be a long-term proposition for logistics providers. Tagging will—and should—move back to the source of production either on the assembly line or embedded in packaging once the technology becomes more mature, reliable and widely used.
RFID tagging for customers is a labor-intensive and costly technology investment for logistics providers. They believe they will achieve a return on their investment only when manufacturers automate the tagging. That would allow logistics providers to cut their own labor costs, by reading tagged pallets and cases automatically as they move through dock doors, instead of manually scanning bar codes. It would also enable them to provide additional customer services by capturing data as goods move through the supply chain.
Trevor Pierce, DHL's RFID program director, says the company's role is not just to help customers fulfill mandates. "We foresee benefits from RFID when we collect goods with the tags already attached or when the supply chain is fully RFID enabled," he says. "We're looking to support our customers who are facing mandates, but there are also opportunities where we can improve upon the services we provide or on our own cost positions."
Ryder Systems of Miami set up a test lab in its Fort Worth, Texas, facility to help clients meet Wal-Mart's mandate. "We have customers coming out of the woodwork," says Steve Hitchings, group director in Ryder's IT supply chain solutions technology services group. But that's not where the company wants to be.
The real return on investment will be in using the technology to drive process improvements through the supply chain, through the integration and sharing of data between logistics providers. Ryder could also see efficiencies once customers move their RFID tagging to the production line. Those savings will be primarily in reduced labor costs. "We'll no longer have to scan bar codes," says Hitchings. "Everything will be done by RFID readers to confirm a shipment in or out the door."
The question, according to logistics providers, is whether customers will pay for better tracking of shipments and more specialized services, such as guaranteeing in-stock positions and delivery times, or ensuring that goods were kept at a particular temperature throughout their journey. It's a big issue because logistics providers would have to invest substantial sums to acquire the capability to provide these services.
The executives interviewed by A.T. Kearney said they see a tremendous potential for the use of real-time data gathered by RFID systems as their goods move through the global supply chain. The majority would prefer to buy the data from a logistics provider as a stand-alone service. That way companies could pay for RFID data collection on select containers, such as those full of high-priced goods or traveling along unreliable trade routes. The report estimates that the data could help firms cut inventory, reduce out-of-stocks and shrink lead-time variance—leading to an estimated savings of $1,150 per container.
Asset tracking is another logical area where logistics providers could achieve a return on investment from RFID. Typically, companies lose a good number of assets each year and write off the losses as the cost of doing business.
Maersk Logistics, along with Maersk Sealand, the Copenhagen-based shipping company, both part of the A.P. Moller-Maersk Group, have been evaluating active and passive RFID technologies in pilot programs. "The company owns thousands of shipping containers, truck chassis, refrigeration units and other assets that it uses to ship customer goods around the world," says Cindy Braun, general manager of the company's RFID Competence Center. RFID could assist in optimizing the management of these assets and reducing the associated costs of idle containers and chassis for both customers and the company.
RFID is already used by some railways in North America to track assets. In the mid-1990s, BNSF Railway started attaching passive tags to its assets and now tracks the location of all 5,000 locomotives and 200,000 freight cars. Janet Galassi, BNSF director of technology services, says the tags are read at 500 fixed locations along the company's 3,300 miles of track. The tracking, while not real-time, pinpoints the location of the last reader the container has passed.
Top Priority: Container Security
Governments, businesses and logistics companies all agree that security is the most important issue in overseas shipping. After the Sept. 11, 2001, terrorist attacks, U.S. government officials became alarmed by the vulnerabilities of the nation's supply chain. The ultimate doomsday: Terrorists could smuggle a nuclear weapon into the United States in a shipping container. An estimated 95 percent of containers are not inspected upon entering U.S. ports.
When A.T. Kearney asked business leaders to prioritize their concerns about the cross-ocean supply chain, Hijazi says he expected they would point to business concerns, such as locating lost containers and reducing out-of-stocks. But container security was the overwhelming response. "That really keeps executives up at night," he says. Executives fear brand damage if their shipping containers or products are associated with an attack.
The U.S. Department of Homeland Security (DHS) has a host of initiatives under way to try to secure shipping lanes and improve security in the nation's ports. The Customs-Trade Partnership Against Terrorism (C-TPAT), for example, is a voluntary partnership between the United States and 9,100 international logistics companies to try to protect the global supply chain from terrorists. In June, the U.S. Customs and Border Patrol announced that there would be preferential treatment, including no routine inspections of shipments, for C-TPAT members who use "smart" container security devices—such as active, battery-operated RFID tags—that can act as a seal on the container and indicate whether the container has been "breach-free" during transit. APL Logistics plans to test active 433 MHz RFID tags as electronic container seals in its trade lane between Singapore and Kaohsiung, Taiwan, as a possible compliance solution to meet U.S. guidelines. The "green lane" could spur the adoption of RFID, by giving logistics companies that comply a competitive advantage.
One question is who will pay for the infrastructure needed to secure the supply chain. Tom Ridge, former secretary of the DHS, believes the federal government will continue to make grants to U.S. ports to beef up security and that some of those funds may be used to build RFID infrastructure. In addition, he says that other governmental bodies, such as the European Union and the World Customs Organization, have funded projects. But Ridge ultimately believes investment in RFID infrastructure will come more from the private rather than the public sector. "The economic motive and the security motive, as it relates to RFID, need to go hand in hand," he says. "It adds value to our operations. It adds security to our operations. It's two for the price of one."
The logistics business has become fragmented and fiercely competitive as a result of 25 years of deregulation and rising global trade. But logistics providers pulled together this year after they witnessed many different industries that they service—aerospace, automotive, consumer packaged goods and pharmaceuticals, among them—adopting different types of RFID technology with the expectation of eventually tracking and tracing shipments.
Logistics industry leaders were forced to start testing applications of the technology in their own businesses and calling for the development of industry standards. "They believed they needed to come together and be a voice that was heard," says John Seaner, vice president of industry development for EPCglobal US. That clamoring led EPCglobal to create a Logistics and Transportation Action Group, which met for the first time in April in Brussels and again in July in Singapore, to determine industry-specific RFID requirements for software and hardware developers.
But creating the architecture of an RFID system in the international logistics supply chain may be complicated for several reasons. First, it will likely involve deploying two different types of RFID technologies. In the private sector, retailer mandates require pallets, cases and some individual items to be issued Electronic Product Code numbers on passive RFID tags. But the cargo containers used in the transportation industries are thick metal boxes that would require active RFID tags; these battery-operated tags are always on, don't suffer from the same interference from metal and liquids as passive tags do and can be read from longer distances. Several companies are testing active RFID tags, which can cost $250 each but often have an operating life of six to seven years.
Another problem stems from the competitiveness among logistics providers. "These folks are looking at it as, 'How do I add value to my business?'" says Seaner. "With scant margins, companies are constantly vying for business."
FedEx, UPS and other companies have their own proprietary tracking systems that allow them to provide value-added services to their customers, including real-time tracking over the Internet. But other logistics providers want one international numbering system so that their interrogators can capture RFID tag information from any company's packaging. In the end, they want shipments to be able to exchange hands from FedEx to APL to DHL to Ryder and provide the seamless ability to track that information for the customer.
Who controls the tracking data poses yet another challenge. As RFID-tagged containers and pallets travel, say, by ship or air and then by truck or rail, logistics providers need to figure out how the data will be shared to benefit all supply chain participants. Time will tell whether the fierce competitors can agree.