May 22, 2020As goods move through diverse channels faster and directly to consumers, the process of cross-docking at warehouses allows products to flow through a facility within a matter of hours. For items that travel in and directly through these warehouses or micro-fulfillment centers, visibility poses a key challenge. Some warehouse personnel scan barcodes, and companies are increasingly deploying passive UHF RFID labels to gain a view into when and where they are received, and to ensure they are quickly reloaded onto the proper vehicle for delivery.
Zebra Technologies has released a solution leveraging UHF RFID that draws from the company's existing products but is customized for the cross-dock environment. Zebra's new visibility solution, MotionWorks Warehouse, is intended specifically to help logistics providers and others in the supply chain gain real-time information about the movement of inventory.
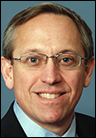
Zebra's Mark Wheeler
The system is designed to enable real-time tracking of equipment and personnel movements, thereby boosting productivity and reducing the risk of shipping errors. For the past year, MotionWorks Warehouse has been in use at a cross-dock site by a large U.S.-based transportation company that helped to co-develop the solution. Zebra is now releasing the commercial version for use at warehouses, as well as for logistics and manufacturing.
The solution leverages Zebra's ATR7000 overhead UHF RFID reader (see New Zebra Reader Promises Real-Time RFID Data Capture) to provide real-time location data at warehouses and manufacturing sites, along with its MotionWorks software to manage the collected read data. Typically, the wide-area readers can be installed in a grid pattern to cover a building or zone, such as a warehouse cross-docking area, to provide real-time visibility of tagged items. In fact, the ATR7000 is designed for real-time location with passive RFID tags.
"It can actually locate a tag within a few feet," says Mark Wheeler, Zebra's supply chain solutions director. "We feel that's a substantial breakthrough for passive UHF in the supply chain." But while the reader has been used since its 2019 launch by different sectors, including warehousing and manufacturing, what's been missing, Wheeler says, is a way to integrate the RFID data captured by the device into a user's existing warehouse operating system. Therefore, MotionWorks Warehouse is designed with an application programming interface (API) to make integration easy.
The system comes with features specifically designed for the cross-docking environment. With the single API and reader deployment, Wheeler says, warehouses will gain visibility into their receiving and shipping docks, down to the particular lane in which they may be located. MotionWorks enables users to view the locations of tagged assets and workers, and to thereby dispatch loading and unloading appropriately, while also viewing the building of a shipment order, and ensuring no pallet is misrouted or omitted from an order.
Traditionally warehouses that have employed RFID tags have often used handheld readers to capture tag ID numbers as goods are loaded or unloaded, or they have installed portals to track the tags that pass through a specific chokepoint. However, Wheeler notes, that only provides visibility into certain actions. With real-time tracking, management could view the locations of inventory or assets throughout an entire cross-dock facility.
This real-time data may be more important than ever, Wheeler adds, as the micro-fulfillment environment is growing, with demands from retailers and consumers for faster turnaround times. Facilities are seeking greater visibility in order to ensure goods are received and then reloaded accurately, without delay, even if the turnaround time is only a matter of hours or even minutes. "They'd love to be able to unload trailer one," Wheeler says, "and have an eye in the sky to see those goods be removed, staged in lanes dedicated to the loading dock, and then packed in trucks."
The increasing prevalence of RFID tags makes that easier, Wheeler notes, adding that some advanced shipping notices (ASNs) may currently come with RFID inlays built in to make automated RFID data capture possible at such sites. An ASN is automatically captured, and related data about that order is then accessed in the software. While such deployments are rare, Zebra has noted that several companies are in discussions about using ASN RFID tags in this manner.
Those interested in deploying the new solution are now planning to use RFID tags to track the movements of assets, such as forklifts, pallets or other equipment, as well as goods that are received and shipped from a site. In that way, a warehouse's management could view where workers and their equipment are located, and appropriately assign work orders for the forklift operators, based on their locations and activity.
The system also tracks where goods are moved and if an error is made. For instance, if an RFID tag is applied to each forklift and carried by drivers in the form of a badge, the system can track the movements of that vehicle and its operator in real time. If pallets and shipments also have RFID tags attached to them, the system knows when goods arrive, where they were routed and who transported them.
That data provides multiple benefits, Wheeler says. For example, the warehouse-management system (WMS) can dictate where each product needs to be routed, including the dock door at which it should be staged and then loaded onto a delivery truck. Data from MotionWorks can identify where the goods are located and when they might be staged for loading onto another vehicle.
The location data is precise enough to indicate the lane in which goods are located, Wheeler reports. If the lane does not correspond with the one intended for a particular pallet's loading dock in the WMS, MotionWorks could generate an alert that could then be viewed by forklift operators or management. The cloud-based data can be shared with other parties, such as shippers or the receiving customer. Those authorized parties could then sign into a dashboard to view when the goods were received, as well as when they were staged or loaded for delivery. Warehouses can also utilize the data on an historic basis to improve their own operations.
The solution can track how long it takes for shipments to be moved. For instance, Wheeler says, MotionWorks "has visibility tools to see the history of material movements in a facility," which could help a manager develop process improvements or better utilize spaces and assets (such as forklifts). "You have a view into how you can lay things out better or improve that process," he states.
Zebra's goal, according to Wheeler, is to make the system faster to install and employ for warehouses that have little time or resources to build an entire solution themselves. "With APIs," he explains, "the application is ready to go and faster to implement," specifically providing material tracking in a cross-dock environment. For warehouse workers, the system reduces their need to repeatedly step off forklifts—to physically scan barcodes, for example. By viewing dispatch orders on a tablet based on the RFID data, they can more efficiently identify which items they need to pick up and where they should be delivered.
Wheeler predicts that with the ease of real-time tracking using low-cost, passive RFID tags, "This might tilt the scale toward RFID use." He adds, "It's the only technology low enough in cost that you can tag once and throw it away." The technology could improve the odds of operators meeting very short transfer times, he says. The company expects adoption from logistics providers, import-export bonded warehouses and manufacturers. It could also be used with reusable ultra-wideband tags.
"You have 24-7 visibility of when materials come and go from a bonded area," Wheeler states. "Things like that are going to be very attractive." The system is currently designed for North American deployments, but it is expected to be released in Europe and Asia in the future as well.