Dec 16, 2015Want to know the temperature of machine parts before they overheat and cause damage? Monitor water-intolerant assets without opening the container to check each one? Detect strain in concrete? Save water while increasing plant growth in greenhouses and crops in fields? Automate the time-consuming process of tracking tire pressure on aircraft?
Passive ultrahigh-frequency RFID sensor tags, introduced in the past few years, enable companies to monitor these and other conditions, because they are not hampered by the limitations of wired or battery-operated sensors. Wired sensors can be bulky and difficult to install and access. They require a power source and can't be used in remote environments. Active wireless sensors have batteries that must be changed on a regular basis, which can drive up costs and interrupt processes.
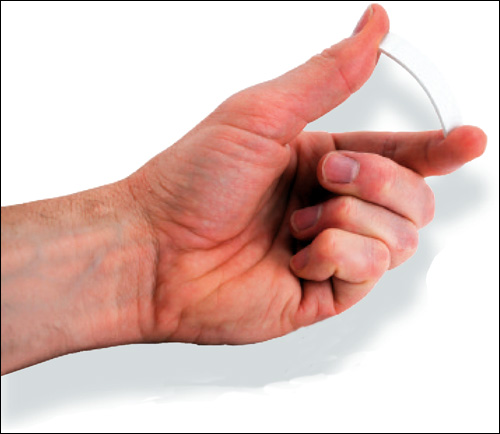
When manufacturing electric motors, for example, companies need to monitor the temperature of motor rotors to ensure they don't overheat and shut down.
Embedding wired temperature sensors in rotors is not an option, because it would prevent the rotor from rotating, says Mikel Choperena, product development manager at Farsens, which offers a variety of passive UHF RFID sensor tags. If a company uses active sensor tags to monitor rotors, he says, it must stop all production whenever a battery is low to take the sensor out and perform a battery change.

Passive on-metal temperature tags, on the other hand, can be attached or soldered onto the motor rotor. RTEC's sensor tags, for example, can be as small as 5.5 millimeters (0.2 inch), says Drex Lee, marketing and sales executive for the company.
Smartrac's Sensor Tadpole, equipped with RFMicron's Magnus S2 integrated circuit, comes in 21.5 by 73.0 by 2.5 millimeters (0.8 by 2.9 by 0.1 inches) and its wet inlay format is easy to implement and works on difficult surfaces, such as metal parts in car chassis, says Christian Achenbach, a Smartrac spokesperson. "The size is thin and small, which is tailored to the demand of car manufacturers or other industries, where moisture detection is an essential part of quality control," he says. "The tag detects small amounts of water leakage inside vehicle compartments that can damage a car's electronics bays, cabins and trunks. Window seals, weather stripping and body seams are the primary causes of factory water leakage."
Passive UHF RFID sensor tags are also less expensive than wired and active options. Prices range from less than $10 to more than $200, depending on the type of sensor and features, such as high-temperature tolerance, rugged enclosures, number of sensors per tag and read range (more on that later). Load cells that monitor pressure, for example, are more expensive than other types of sensors, Choperena says.
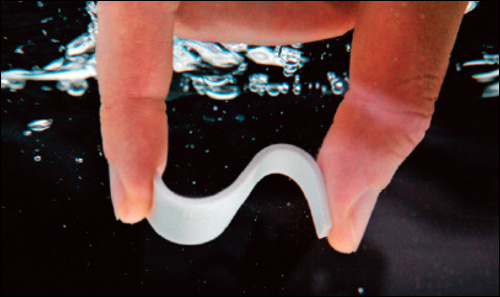
That means it's cost-efficient to monitor the moisture level of soil in large fields for real-time irrigation control. A Farsens RFID sensor tag used to monitor soil moisture costs €15.50 ($16.87) for 500 units, Choperena says. "Most of our projects are R&D investments for our customers, and they want to keep everything confidential until they finish all developments," he notes.
"I was recently at a plant where they were using slip rings to connect wired sensors to rotating equipment," says Scott Dalgleish, CEO of Phase IV Engineering, which offers UHF sensor tags, as well as low-frequency, high-frequency and battery-assisted versions. "These slip rings can cost thousands of dollars, and they provide poor signal quality and are a high-maintenance item. With several $89 UHF RFID temperature sensors, the temperature on the rotating equipment can be accurately monitored wirelessly and never needs to be maintained."
Providers of passive RFID sensor tags say companies in a wide range of industries are interested in monitoring the conditions of their assets, products, buildings and machinery, to reduce costs, boost production and improve safety. RFID sensor tags can monitor ambient light, humidity, moisture, pressure, proximity, resistance, strain, temperature, tilt, weight and voltage.
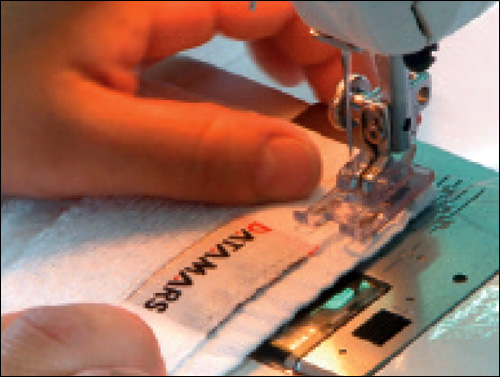
What You Need to Know
RFID sensor tags are versatile, Dalgleish says. "They can be mounted on high voltage, and they can monitor spinning things," he says. "All these things are possible because the sensor can be read wirelessly about every second and never wear out." Monitoring without interruptions to change batteries can mean huge cost avoidance, he adds. In an industrial application such as monitoring production equipment, an unexpected failure can cost hundreds of thousands of dollars.
In aerospace, passive sensor tags that measure pressure can monitor the inflation of airplane tires on a regular basis. Manual pressure checks can take roughly an hour to complete for a single aircraft, compared with a matter of seconds using sensor tags and a handheld RFID reader. Crane Aerospace & Electronics, for example, offers the SmartStem wireless tire-pressure monitoring system, which includes Phase IV Engineering passive sensor tags and readers.
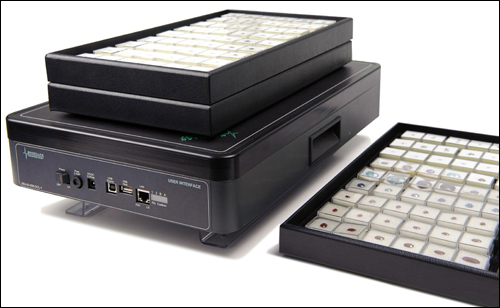
In construction, two potential uses for passive sensors are monitoring deformation, and monitoring bending in pillars and beams used in tunnels, bridges and buildings. Customers are looking into using strain sensors to monitor deformation and accelerometers to monitor variation in structures over time, Choperena says.
Some sensor tags are designed for harsh environments. RTEC, for example, provides tags that can withstand high temperatures, Lee says. Other RTEC tags are waterproof, protected by industrial plastic material or embedded in metal casing.
Phase IV Engineering offers an in-pavement moisture-sensing tag that can be buried in asphalt, and a sensor tag designed for high-voltage bus bars that has a high-temperature plastic lid to withstand temperatures of more than 200 degrees Fahrenheit. "We are also encapsulating some of these sensors in special plastics for use in aerospace applications, where the fluids used, such as hydraulic and brake fluid, are highly abusive to materials," Dalgleish says.
For some applications, passive UHF RFID sensor tags do require maintenance. "Strain gauges [used to measure the strain on an object], for example, lose accuracy over time and need to be recalibrated," Choperena says. And, he adds, most chemical sensors have a limited life because they rely on chemical reactions. "When the sensor runs out of the required components to react to the targeted component, it will stop measuring," he explains.
Most UHF RFID passive sensor tags are compatible with EPC Gen 2 RFID handheld readers. "UHF sensors have a read range of about 6 to 10 feet in open air and 3 to 6 feet when metal-mounted," Dalgleish says. The longer read range would enable an organization to monitor the temperature of high-voltage conductors, he says. HF, LF and Near-Field Communication sensor tags have read ranges of only a few inches.
The size of the sensor tag and how it performs on metal is dependent on the antenna used, Choperena says. "In general, the bigger the antenna, the longer the communication range," he says. "Different antennas can be designed, both smaller or bigger, without any problem at all regarding the size. The issue is the performance you need versus the size of the antenna."
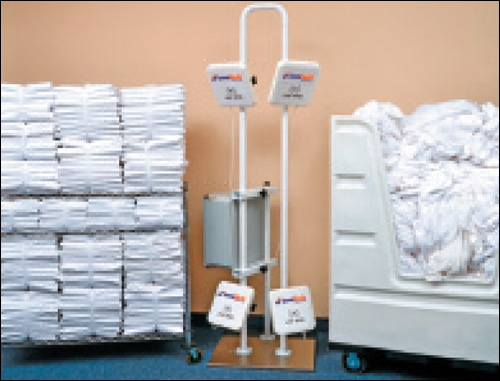
The read range also depends on the output power of the handheld, says Charles Greene, chief operating and technical officer at Powercast, which co-developed passive sensor tags with Vanguard ID Systems.
Another consideration is whether any kind of software is available with the sensor tags, and if so, what functions it provides. Phase IV Engineering, for example, offers "Reader Assistant" software, which runs on a Windows PC. It controls the readers the company provides with its sensor tags, and allows users to do a "read now" of the sensor or "read every x seconds," Dalgleish says. The data can be logged to an Excel file so users can verify the system is getting the readings they need.
"This allows new clients to try the system in a proof-of-concept mode before they do a full integration of the RFID system," Dalgleish says. "The software reports sensor identification number, sensor readings, number of reads, percentage of successful reads and other information that helps the user configure the system to get the data they need."
One drawback of passive UHF RFID sensor tags is they can't log data. The need for data-logging capability ultimately depends on a company's applications, requirements and environments, Lee says. "There are many that don't require data logging," he says.
Special Needs
Passive UHF RFID sensor tags can be customized to meet specific requirements. Vanguard ID Systems, for example, offers standard passive tags that are slightly larger than a credit card, but it can design custom-sized tags to meet customers' needs, says Alan Neves, global RFID account manager.
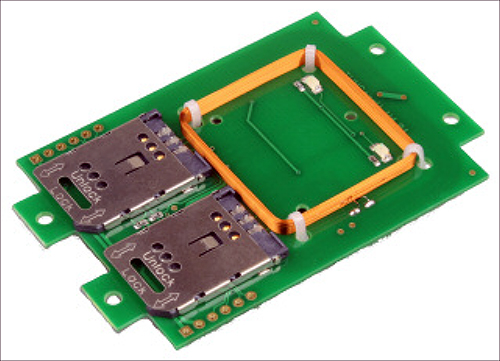
Some sensors can be adjusted to meet specific needs. "End users often have special requirements for sensors," Smartrac's Achenbach says. Based on the application, users can set or adjust the humidity measurement range on the Sensor DogBone moisture-sensing passive UHF tag.
"We have tuned our sensors' performance and sensitivity to be suitable for many [customer] applications," Achenbach says. "Sensor tuning is made by modifying antenna design, which also has an influence [on] read range. Antenna design determines if a sensor is very accurate and can recognize small changes in the environment or can measure large changes in the environment but be insensitive to small changes."
Still, some solutions require ingenuity. To help make the International Space Station's Urine Processor Assembly more efficient, Phase IV designed a system to capture temperatures from a spinning drum. It used an epoxy encapsulating material that could both mold the sensor tags to the surfaces of the drum, and protect the tags from the sulfuric acid and other chemicals added to the urine (see Solving NASA's Water Problem).