Jun 30, 2009Australian telecommunications company Telstra has completed an RFID trial that, if rolled out across its 130 retail outlets, could save the firm up to AU$4 million (US$3.2 million) in annual labor costs and product shrinkage. In the three-month trial—one of the country's largest item-level trials—Telstra tagged the packaging of 12,800 mobile phones, then tracked them from its Sydney distribution center (DC) to six retail outlets around the nation.
Using the RFID system, Telstra indicates that it improved its inventory accuracy through increased visibility from 65 percent to 99 percent. The company also reduced the time it spent receiving goods by 75 percent, the time spent on stock-taking by 50 percent and the time spent searching for missing items by 50 percent. The reduction in shrinkage, combined with labor savings generated by the reduced time spent taking stock that will free up staff members to serve customers on the sales floor, is expected to save the company up to $4 million per year.
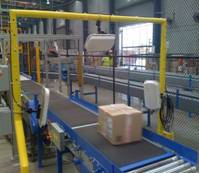
Telstra Enterprise & Government, the firm's network-based solutions and services arm, developed the system and could roll it out across Telstra's retail stores as early as next year.
Julien Marchand, Telstra's project manager, says the trial—first proposed by the company in 2006 (see Telstra Takes On Two RFID Trials)—was held between October 2008 and February 2009. Miami-based supply chain management firm Brightstar, which manages Telstra's DC, had approached Telstra's retail arm, urging it to trial RFID to improve visibility within the supply chain. "The main reason given," Marchand says, "was to reduce the loss of mobile phones in the supply chain, and shrinkage at Telstra retail stores."
In 2007, the total value of retail shrinkage in Australia was AU$2.26 billion (US$1.8 billion), an average shrinkage rate of 1.39 percent of sales. Since phones are high-value items—with Telstra's ranging in price from AU$150 (US$121) to AU$1,000 ($805)—better supply chain visibility could reduce shrinkage.
In launching the trial, Telstra prepared a set of key performance indicators to be met, such as the time spent receiving goods in store, stock-taking and searching for missing phones. Telstra Enterprise & Government worked with NEC to develop the system for the trial. An RFID smart label featuring a passive ultrahigh-frequency (UHF) EPC Gen 2 tag operating at 920 to 926 MHz was attached to the packaging of some 12,800 mobile phones.
RFID interrogators were then installed in the DC and six retail outlets. Telstra experimented with a number of set-ups in order to determine which provided the best read rates, including placing readers at the retail store's stock-room door and entrance ceiling, at the stock-room door and entrance gate, and at the stock-room door and point of sale. "The preferred set-up for read-rate performance and aesthetics purposes," Marchand says, "was putting the readers at the stock-room door and on the ceiling at the entrance, with the readers integrated into point-of-sale IT systems."
All readers connect to a central server, and information is sent over Telstra's own LAN or Next G network. Information is made available to the staff via a Web-based portal Adaptive Asset Manager (AAM), designed by NEC and customized by Telstra Enterprise & Government, thus providing Telstra with immediate access to such data as inventory levels, goods lost in transit and transit time—which, in turn, could trigger alarms for such events as delayed delivery or out-of-stocks.
The immediate benefits were dramatic, Marchand says, with the automated capture of all items passing through the various read points resulting in visibility of up to 99 percent of all items shipped, received and moved within the stores.
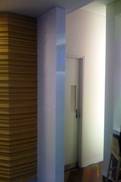
There was also a reduction in time spent investigating in-store shrinkage. Traditionally, employees would have to search the stock room and watch days of CCTV footage to determine when and where a phone went missing. With RFID, however, workers could determine exactly when the phone was last seen in-store, and check the appropriate CCTV footage.
According to Marchand, with the reduction in non-customer-facing time across 130 stores, combined with the reduction in shrinkage, Telstra expects to save up to AU$4 million (US$3.3 million) per year, and a positive return on investment within 18 months. "We also expect some long-term gains, such as reducing the time we are out of stock and increasing sales," he states, "but we need more time to see those benefits because we need to adjust our processes accordingly, as we are seeing things that we didn't see before."
All Telstra retail stores are in the process of refreshing IT systems, Marchand notes, so the company will have to wait until that is finished. Telstra then plans to "strongly consider full rollout of RFID across all 130 stores," he says.
In the future, Telstra Enterprise & Government hopes to provide the complete RFID system to other retailers as a fully managed service. Marchand hopes more Australian retailers will begin announcing the results of item-level tracking trials to increase take-up of RFID across the country. "I really believe we need to hear about more from other companies," he says, "because the savings from RFID will only come when companies begin to share information and learnings. The next step, for us, is to get phone manufacturers to start tagging items themselves, and they will be more likely to adopt it if they hear of others' successes."