Jun 26, 2009Marigold Industrial manufactures protective gloves for workers who handle such things as sharp knives, harsh chemicals or frozen packages. To get better visibility of the materials used to construct those gloves, and to improve its ability to track the finished products, the company has deployed an RFID system based on passive EPC Gen 2 RFID tags and interrogators at its manufacturing facility in Poiares, Portugal.
The new system, which replaced a paper-based tracking process early this year, is increasing the accuracy of inventory and shipment records within the facility. Once fully optimized, Marigold indicates, it should also decrease the amount of time required to complete inventory counts. CreativeSystems served as the project's systems integrator.
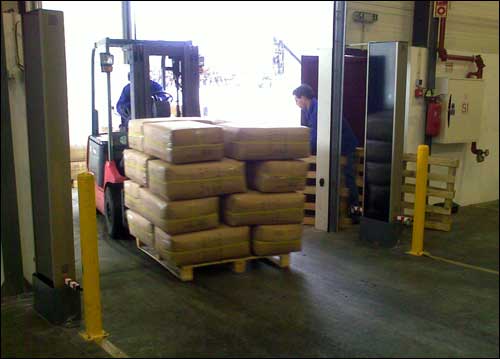
As pallets loaded with boxes of materials and components—such as various grades of rubber and cloth—arrive at the factory, Marigold's employees key in the corresponding purchase order number into a computer linked to an RFID label printer-encoder. Software known as Backoffice, developed by CreativeSystems, runs on the computer and communicates with the SAP enterprise resource planning (ERP) software used by Marigold. The ERP software pulls up the order details associated with that purchase order, then this information is sent to the Backoffice software, which generates an RFID label for each expected box of material or components.
Inside each label is an Avery Dennison RFID inlay made with an NXP Semiconductors UCode EPC Gen 2 chip. Backoffice assigns a unique ID number that is encoded to the chip and associated with the order information.
A worker places an RFID label on each box within the shipment. The boxes are then moved through an RFID reader portal on the dock. As this happens, Backoffice logs the incoming shipment data and reconciles it with the purchase order information. If the number of boxes does not match the number indicated on the purchase order, the software sends an alert so that workers can find and reconcile the discrepancy.
After being placed into the warehouse for storage, the tagged boxes of materials are inventoried once per month. Prior to deploying the RFID system, employees had performed weekly manual inventories of the warehouse stock, so the new technology has already reduced labor hours. However, Miguel Roxo, Marigold's RFID manager, says he and his staff have encountered problems reading some of the tags placed on these cases, and are presently working to improve the read rates.
"In the beginning, we were placing the RFID labels anywhere on the boxes, and then placing the boxes on pallets before putting them into the warehouse," Roxo explains. "When we then went to read the tags using an Alien Technology EPC Gen 2 handheld reader, we found that some of the tags could not be read because they were placed on the sides of boxes that were facing inwards on the pallet."
Marigold is also utilizing the RFID system to track its manufacturing and shipping processes. When the factory receives a glove order from one of its customers or distributors, the software directs workers to pull the boxes of materials and components necessary to fill that order. The RFID labels on those boxes are read as they pass through a portal reader located between the warehouse and production area, and the software tracks this movement so that managers can see how many boxes of a given material are being used in production, and can calculate the number remaining in storage at any particular time.
Once the materials are made into gloves, the finished products are placed in boxes (with a standard quantity of each product per box) that are tagged and tracked using RFID, in a manner similar to how the materials are tracked. A worker logs into the ERP software and pulls the current order information, then associates that data with the type and quantity of product that has just been produced. RFID-enabled shipping labels are then printed, through Backoffice, for each case of finished goods. A unique ID number is created and encoded to each inlay, and associated with the customer's order.
The tagged cases are then brought directly to the shipping dock, where they are placed on pallets for shipment. Distributors that purchase Marigold Industrial's goods and sell them through various channels pick up some of the finished product. The remaining orders are shipped to a distribution center (DC) operated by Marigold, which the company uses to stage orders before they are shipped to customers.
Before being placed on a truck, each pallet is placed on a shrink-wrap machine, where it rotates as the film is applied over the cases, in order to ensure that the pallet is secured during shipment. While the case rotates, an RFID reader mounted nearby captures the ID numbers of the RFID tags on all cases.
Backoffice than compares the tag ID numbers and its associated product information with the packing list, to ensure that all of the products required to fulfill the order are present, and in the correct quantities.
At this time, Roxo indicates, the RFID tags are used only for internal purposes at Marigold's Poiares factory, though he says his company eventually hopes to install interrogators at its DC, so that the RFID labels can be utilized for identifying and tracking the orders coming into and out of that facility.