Jun 06, 2008Gelal, Europe's largest sock manufacturer, claims it has seen a 40 percent improvement in productivity at its Istanbul manufacturing site, thanks to an RFID-based tracking system, according to Stephen Crocker, director of channel management for Alien Technology's European market. Gelal is employing EPC Gen 2 UHF tags and readers made by Alien, replacing an existing bar-code process that required manual scanning.
Gelal produces 200,000 pairs of socks each day. The company's name may not be widely known, but the same can not be said of Adidas, Nike, Reebok and other brands for which it makes socks. The manufacturer used to transport the socks between production stations—where dyeing, sewing and other steps are carried out—inside large cloth sacks, which workers would identify by manually scanning a bar-coded label attached to each bag. The scanning required significant time to carry out, however, and also occasionally caused production backups when the labels became bent or smudged, making them difficult to read.
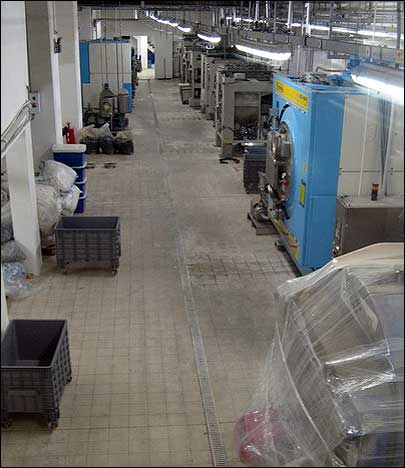
Now, the socks travel inside plastic totes, to which passive EPC Gen 2 tags have been attached. Gelal has mounted an Alien ALR-8800 reader at each of its 20 production stations. As a particular tote is wheeled to a production station, the interrogator reads the tote's tag and sends its unique ID to the enterprise resource planning (ERP) software the company uses to guide workers through their production steps (the same software the company employed under the bar-code system).
At the beginning of the manufacturing process, a tag's unique ID is associated in the ERP software with the production order for the specific socks that the tote will transport between work stations. Once workers complete a production step, the software tells them where next to send the tote. After the production process is complete, the finished socks are removed from the tote, which is then reused.
Gelal began investigating RFID 18 months ago, and has had the new production tracking system up and running, with 20,000 tagged totes, for the past six months. According to Crocker, the transition has lowered the firm's labor needs enough to cut the number of personnel required for each production shift from 20 people to 12.
To deploy the system, Gelal worked directly with its ERP provider and systems integrator, Sayilgan Software, and STS Technology, a hardware distributor that is a channel partner for Alien in Turkey. Sayilgan adapted its ERP software to control the interrogators, Crocker says, by utilizing Alien's application protocol interface.
Gelal has been employing Alien's ALN-9554 M passive tag, designed for use on totes and other reusable assets, but Crocker says the company soon plans to switch to the Alien ALN-9562-SH, or "Short Squiggle" tag, because the smaller size of the ALN-9562-SH enables it to be converted into an ISO-compliant card roughly the size of a credit card. Gelal wants to use the ISO-compliant card form factor due to its standardized size.