Jul 18, 2017A year ago, at the request of potential customers, Invengo Textile Services developed a mobile app-based, RFID-enabled linen-tracking system for hotels or hospitals as a low-cost extension of its Acuity real-time visibility solution. Now, the company reports, having proven its success in those early installations and having built business analytics for the cloud-based service, Invengo is offering the solution to customers worldwide.
Acuity Connect enables companies such as hotels—whose laundry services providers already employ Acuity to manage their linens—to use the technology for their own purposes. These include tracking towels, bedding or uniforms as they arrive at the facility, and when they leave.
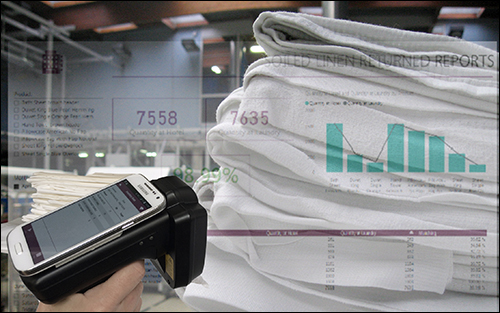
Since 2012, linen service providers across Europe have been using the Acuity system to better manage their inventory. Approximately 10 million tags are currently being tracked on linens daily across the continent with this system, says Fabrice Morini, Invengo Textile Services' sales VP.
The linen service providers typically own the towels, bedding and other linens, as well as some uniforms, that its customers in the hospitality and health-care sectors use. These customers sign contracts to pay for the use of the linens for a specified period of time, and the laundry and linen service company picks up the items when they are soiled, washes them at its own laundering site and returns them to the customers, who pay monthly fees for the service.
However, the company notes, tracking these products is a difficult task. Typically, about 30 percent of inventory is lost each year, though how it was lost, or who was responsible, can be difficult to identify. Large or busy laundry services cannot count every item as it arrives in a cage, soiled or wet, from a customer—and while some companies have used bar codes to track inventory, individually scanning each item can also be time-consuming.
With the Acuity system using EPC UHF RFID tags, Morini explains, a cage with up to 500 items can be read as it passes through a portal at a dock door for soiled linens and through an RFID-enabled cabin for clean linen checkout and shipment to customers. The technology helps the linen service companies to identify when products are lost so they can address the problem, and also saves manual labor time employees would otherwise spend counting linen items.
Customers of these linen service providers began asking for a solution that would allow them to take advantage of the RFID tags already attached to the products they use. "We had end users asking us for better visibility of their stocks," Morini states.
A year ago, two companies deployed the technology at multiple hotels throughout London and Paris. Invengo began further developing the app and business-analytics software, and the company is now releasing the function as Acuity Connect.
Companies can purchase the solution from the linen service providers, or directly from Invengo. They can also use Invengo handheld readers, or those from ATID or other technology providers. Invengo provides the Acuity Connect app, which can be downloaded on an Android- or iOS-based smartphone or tablet.
When a linen provider delivers clean linens to the hotel, employees use a handheld reader that can be waved above or near the cage to capture all items in that load. The handheld reader typically forwards that data to the user's mobile phone via a Bluetooth connection, and the app on the phone then updates the inventory count to indicate which items have arrived and are now considered available for use.
Hotel managers can utilize that data to dispatch the linens to the appropriate locations, such as specific floors. With the app and a handheld reader, personnel can update the items' locations as they are sent to a certain floor, for instance, or to a linen-storage area.
When soiled linens are sent back to the service provider, the hotel employee can use a handheld device once more to read the tags of the items being sent for laundry services. In that way, the hotel has an up-to-date inventory list of what is onsite.
If the hotel chooses to share its data with the laundry service provider, it could also forward the data to that company regarding what specific items are being sent back for laundering. The service provider could then use that information to create a replenishment list. The hotel can also conduct inventory checks by dispatching a worker with a handheld reader through the rooms and storage areas to identify what linens are on hand, and which ones may have gone missing.
The benefits for hotels can be found in the analytics, Morini says. For instance, a company using Acuity Connect can not only ensure that it never runs out of linens, but also identify when it has linens onsite that are not being used. In that way, the hotel and the service provider can better optimize what products they keep onsite, and thus order more or fewer of specific items accordingly.
At present, 25 to 30 laundry service providers across Europe are using the Acuity system, and many hotels could use the tags already on the products they receive from those companies. Invengo sends its EPC UHF laundry tags to its customers' linen manufacturers, so that they can be applied as products are being made.
Since each RFID tag has a unique ID number encoded on it, the linen company—and now the hotel as well—can use that tag to track the product's lifetime. This includes such details as when an item was manufactured, how often it was laundered and when it needed to be discarded.