Aug 23, 2016For the past four years, VarodaRent, a Dutch company that provides containers and other moving equipment on a rental basis, has been using radio frequency identification technology to track the movements of its boxes, containers and other assets as they are automatically sent to customers and then returned. The company is now deploying the same RFID solution, provided by Belgian company Aucxis, to two more facilities at which its half-million assets will be tracked. The system consists of EPC Gen 2 passive ultrahigh-frequency (UHF) RFID tags, handheld readers and Aucxis Base Gates, each of which contains a fixed RFID reader with four 30-degree antennas.
VarodaRent was founded in 2011 as a spinoff of Dutch moving company P.A. van Rooyen, to rent out reusable plastic containers used for moving and storage—including some measuring up to 20 feet in length—as well as small packing boxes and dollies. The firm has approximately 500,000 assets in about 100 different categories, says Patrick Schoonenberg, VarodaRent's general manager, and the number rented out at any given time depends of the time of year. "In busy times," he states, "it is up to 80 percent." One of its primary customers is P.A. van Rooyen itself.
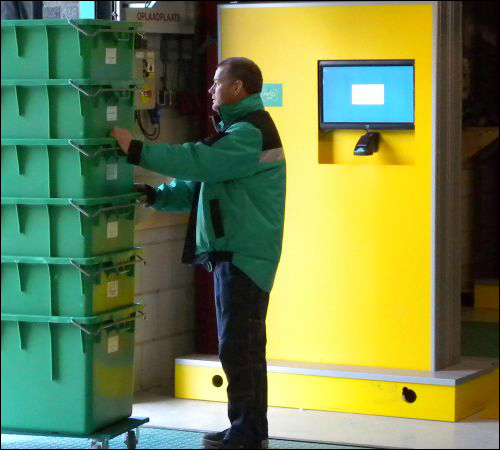
Prior to installing the Aucxis RFID system, VarodaRent tracked its assets manually, using paper and pen. When a customer's order arrived, the company delivered the requested containers via one of its own vehicles, or the customer picked up those items at the VarodaRent facility in Uithoorn (near Amsterdam). An employee recorded that transaction by hand and then input the information into the computer.
As the business became busier and the volume of containers increased, the manual method of tracking grew more difficult to manage. "We did find out that it is very hard to count correctly," Schoonenberg says, "or to see the difference between articles that look the same." For instance, some plastic boxes are identical other than one having nylon wheels and another rubber wheels. "This was the main reason, at first, to start up RFID."
The company also found that it was difficult to trace the point at which goods went missing if a customer failed to return an expected number of products, or claimed to have not received everything that had been ordered.
Four years ago, VarodaRent began working with Aucxis, which recommended a software suite in which customer orders could be inputted. The software would then track the tagged items as warehouse workers pulled and shipped them, and issue an alert if a mistake were being made.
So in 2012, VarodaRent began attaching RFID tags to its containers and equipment, a process that took approximately three months to complete. The tags in use vary depending on the material to which they are attached. (Aucxis works with a variety of tag providers, including Smartrac and Omni-ID, but declines to name the specific makes and models of tags being used by VarodaRent.)
Here's how the system works: When a customer places an order, the Aucxis software lists the items requested. Staff members then print out a form listing the ordered products, as well as a bar-coded ID number. Warehouse personnel bring the paperwork into the facility and collect the items for that order, using Nordic ID Medea handheld RFID readers to interrogate each item's tag.
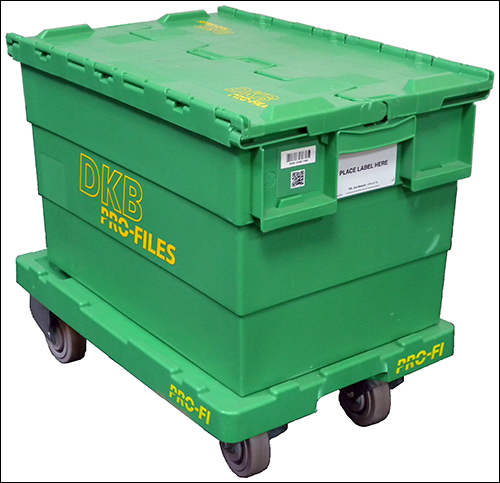
Workers stage the items in the loading area, then scan the order form's bar-coded ID number and begin moving RFID-tagged goods through a Base Gate installed near the dock doors. In that way, each product moving through the portal on its way to a truck is identified via the reading of its RFID tag. The reader captures the ID encoded on the tag, then forwards that data to the Aucxis software residing on VarodaRent's server, where the tag ID is stored with the product's description and serial number, and is linked to that particular order.
If the system reads a tag attached to an item that that should not be in a particular order, an alert sounds on a computer screen where the software is running, thereby warning warehouse workers that there is a loading problem that needs to be addressed.
When containers or other rented items are returned, their tags are again read as they pass through the Base Gates at the dock doors, and those items are automatically credited in the software as being returned. In the event of an error, such as a customer returning an unrented item, the system sends a text-message alert to VarodaRent's management.
In addition, drivers utilize Medea handhelds, using Aucxis customized software to manage read events, to read tags as items are offloaded at a customer's site. The devices are also used at VarodaRent's warehouse to read tags on 20-foot containers.
With the system in place, the company now automatically collects a record of what has been sent to a customer, as well as when those items are returned. The company can thus more easily identify when something has not come back and needs to be invoiced.
VarodaRent reports that it is saving about 40 percent of its administrative labor hours by using RFID technology, as well as 60 percent of its bookkeeping hours. The sales rate has increased as well, the company indicates.
Because the Aucxis system makes it possible for VarodaRent to know exactly which products are within its warehouse at any given time, the company has also begun making this information available to its customers. Some have a password enabling them to sign into a portal on VarodaRent's website to view which items they are currently renting, access archived orders they placed in the past and book similar orders. The company says it is also utilizing the data to better plan the use of its 28 trucks, and its 100 drivers and packers. By tracking the historical data of rented goods, the company can now assign trucks and employees to better match customer demand.
Within the next few weeks, the firm plans to open two more facilities—one in the northern region of the country, the other in the western section. Base Gates will be installed at these locations as well.
Currently, Schoonenberg says, the software resides on VarodaRent's own server. As the RFID solution is expanded to additional facilities, however, the company intends to reassess whether to continue hosting the software or using a cloud-based server.