Dec 07, 2015French sporting goods retailer Decathlon says its sales increased by 11 percent last year, and attributes part of that growth to an ambitious radio frequency identification deployment at all of its 951 stores worldwide, as well as at approximately 43 warehouses (logistics centers). During the same time period (2014), the company experienced a 9 percent reduction in shrinkage, says Jean-Marc Lieby, Decathlon's RFID project leader. Most of the stores are now using RFID technology for inventory checks at the point of sale and at security gates. The company's stores in India and Brazil, however, are using RFID only for tracking inventory. As the firm opens new stores around the world, those sites will also become RFID-enabled.
The retailer credits about 2.5 percent of the sales increase to improved stock availability due to the RFID-based inventory-tracking system. However, the company adds, the launching of new stores and decreases in the prices of some of its merchandise also played a role.
Decathlon is one of the largest sporting goods and sportswear retailers worldwide, with a presence throughout Europe, as well as in China, Morocco, India and Brazil. The retailer ships 650 million items annually in a total of 50,000 containers. About 85 percent of the products are eligible for RFID-tagging, Lieby says.
The stores themselves vary in size and in the merchandise they carry. They typically measure 1,000 to 12,000 square meters (10,800 to 129,000 square feet) in size and offer an average of 35,000 different items for sale, covering 65 different sports.
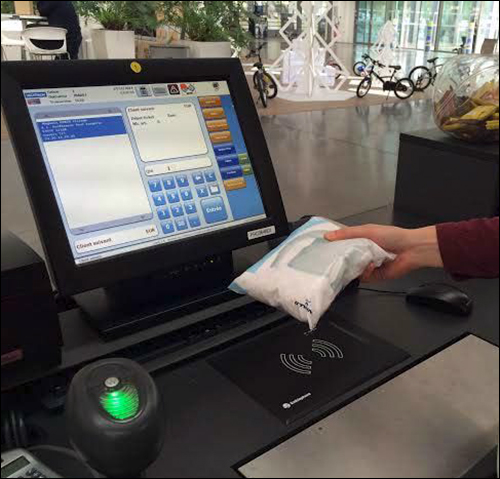
About five years ago, Lieby says, the company began investigating ways in which EPC ultrahigh-frequency (UHF) RFID technology could improve inventory accuracy across its many stores and logistics centers, thereby ensuring that products were on store shelves when customers needed them. That effort was led by Patrice Ribout—who, at that time, served as the RFID project's founder and coordinator, and as the RFID leader at Oxylane Group, Decathlon's parent company. According to a Decathlon survey, the first source of dissatisfaction for a customer is always the same: failing to find a product on the shelf. The company was also interested in enabling faster and easier transactions at the point of sale for shoppers, and thus began researching how RFID tags on products might make that possible as well.
After researching various RFID companies and the solutions they offered, Decathlon launched its own RFID firm in 2010. That company, known as Embisphere, designs, manufactures and deploys both RFID software and hardware, not only for Decathlon but for other retail customers as well.
In July 2013, Decathlon began applying tags to all of its Passion brand products in the factories, and then tracking those items through some distribution centers and into RFID-enabled stores. Beginning in spring 2014, nearly all of Decathlon's other products were tagged at its logistics centers and then tracked as they left those centers, as well as in the stores.
By the second half of 2014, more than 800 of Decathlon's stores were fully RFID-enabled and had changed their processes to include reader use for inventory counts, sales transactions and electronic article surveillance (EAS) security gates. All goods manufactured by Decathlon are RFID-tagged at the factory (merchandise not made by Decathlon is tagged at the logistics centers). The logistics centers are using Embisphere readers in multiple ways, including reading the tags of goods as they arrive in cartons as well as when they are shipped to a store. Decathlon also applies RFID-enabled EAS hard tags supplied by Checkpoint Systems and a variety of other vendors to high-value items that are at high risk for theft.
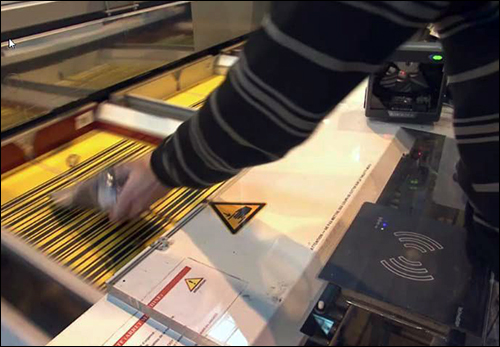
Embisphere is in charge of Decathlon's RFID label management efforts, including the selection of label suppliers, as well as overseeing the quality-control and multisourcing of those labels. Embisphere also defines and specifies the technical solutions in stores and logistics centers.
Decathlon's stores are utilizing RFID labels provided by three suppliers: Checkpoint Systems, Avery Dennison and SML Group.
Checkpoint announced its partnership with Decathlon in November. The company says it can deliver RFID labels to Decathlon locations within five days of an order. Su Doyle, head of Checkpoint's RFID industry programs, says her company offers inlay design and testing services in North American and European RFID labs, as well as tag production plants located close to manufacturing centers. Checkpoint also features an automated ordering system, Doyle says, "that connects retail brands directly with suppliers and is accessible from any smartphone or Web browser."
Once an RFID label is applied to an item, its encoded ID number is linked to that product's stock-keeping unit (SKU). That information is then stored in Decathlon's own software dedicated to the RFID-based inventory-tracking data.
Employees at some logistics centers use an Embisphere reader on a moveable cart that can be rolled through rows of products in order to capture inventory updates. Some logistics centers also have an Embisphere reader installed at the sorter, where workers place goods that are then packed in cartons for specific store shipments. That reader can capture the items' tag IDs and forward that data to the software, so that personnel can view whether they are shipping the correct products to each store.
At the stores, employees use an Embisphere handheld to perform inventory counts. The reader, which is shaped like a small badminton racket, is lightweight and has a long handle so that it can reach high shelves easily. Workers each carry a smartphone, and the reader transmits its read data to the phone via a Bluetooth connection. Those store associates can then pass the device over each shelf of goods and view the inventory count on their smartphone, and the phone forwards that data to the inventory software on Decathlon's database.
Every store also has a "cashing" system in which an Embisphere reader is built into each point-of-sale terminal. At the cashing stations, workers receive goods from a customer and place them above the reader, which captures all tag IDs simultaneously. Bar-code labels are scanned only for the 15 percent of Decathlon's products that are ineligible for RFID. If there is an EAS hard tag present, that tag is removed via a detacher at the point of sale, and can then be reused on other products.
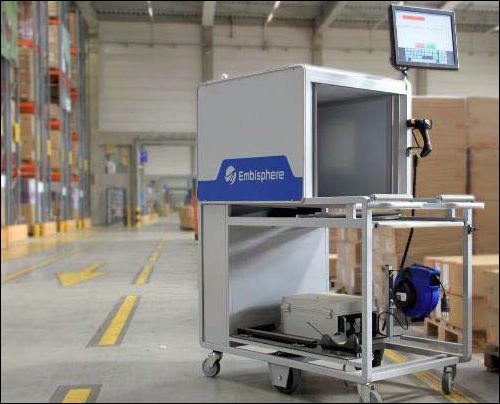
Upon leaving the store, shoppers walk between antennas at an RFID and EAS gate. Checkpoint and Nedap are both providing reader and antenna hardware for the gates. Checkpoint reports that Decathlon has installed Checkpoint's dual-mode Evolve Exclusive E10 RF- and RFID-based antennas throughout 19 countries. Nedap announced in June that its hybrid RFID and RF EAS gates have been installed in 415 Decathlon stores across 15 countries. Stores that had Nedap EAS gates that were installed prior to the RFID rollout were upgraded with a clip-in Nedap RFID reader, while new stores were equipped with hybrid RFID-RF gates from the outset.
Each store's electronic article surveillance system detects any EAS hard tags that pass through the gate, while at the same time, the RFID soft tag is interrogated and its data is transmitted back to the software, which determines if that item has been sold. If all goods were purchased, the customer can simply walk out of the store. If not, the security system prompts an alarm that will warn that individual to stop.
The RFID deployment at all stores was accomplished between March and June of 2014. The company took about one month within that time to train each store's workers. "This was not so simple to organize," Lieby says, since the deployment was being carried out throughout 17 countries, with a variety of languages spoken. However, he says, staff members responded well to the new technology and understood the value it provided.
According to Lieby, the technology has not only improved stores' inventory accuracy (although the improvement varies from store to store and from one country to another, depending on whether the RFID technology is being used as intended), but also reduced labor on the part of workers who track inventory. Most stores can now conduct inventory checks five times faster than they did manually, and these locations are performing inventory checks about twice as often. The retailer is now studying new use cases related to RFID technology, though it declines to identify any specific plans. "What's important to us," he states, "is improvements for our customers and team members."