May 12, 2015The University of Tennessee (UT) Medical Center, in Knoxville, plans to expand its use of a radio frequency identification system for tracking equipment trays and consumables within all of its 36 operating rooms. The solution, known as Continuum OR, was designed by health-care products company DeRoyal Industries, also based in Knoxville, in partnership with the UT Medical Center. Five of the hospital's ORs are already using the technology to track every item used for each surgery, based on a reading of the RFID tag on that item's wrapper as the tagged packaging is thrown into a trash bin. The UT Medical Center is also considering the use of fixed and handheld readers to perform inventory counts of medical supplies stored on shelves in its operating rooms, and to record which surgical supplies are being used on each patient.
All 36 operating rooms are expected to be equipped with RFID by fall of this year.
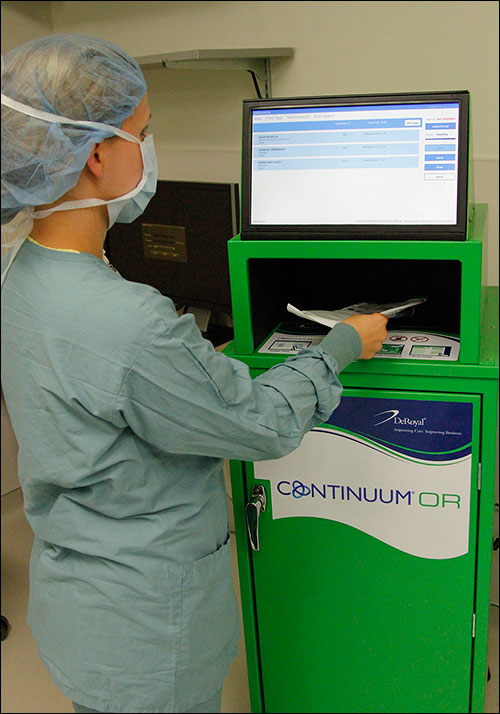
In the meantime, DeRoyal Industries is marketing the Continuum OR solution, consisting of its own software, readers and tags, as well as integration, for other health-care providers. The system was designed to better ensure that the correct supplies and tools are sent to a surgeon for each surgical procedure, and to document that the proper items were used with each patient during the surgery. By the end of the year, UT Medical Center expects to begin using the system for billing patients for the products used in their operations as well.
UT Medical has 36 operating rooms, including five dedicated to orthopedics. A total of 100 surgeons conduct approximately 14,000 procedures there annually, of which 4,000 involve orthopedics.
Like most hospitals, UT Medical traditionally has used a doctor preference card system to equip each OR with the right equipment and supplies. The doctor tells hospital personnel which tools he or she needs for each kind of surgery, and on the scheduled day of the procedures, staff members collect those preferred items, as printed on the preference cards, and send them to the appropriate operating rooms, along with the printed cards. About 50 percent of the supplies sent to the OR are returned unused, and must be put away for another procedure. Conversely, items sometimes are not in the OR when needed during a procedure, leading to delays as employees search for them. What's more, the staff must manually check that items have not reached their expiration date.
"We wanted to completely redesign the system" of managing supplies in the OR, says Becky Ashin, the VP of UT Medical's Advanced Orthopaedic Center.
In 2013, UT Medical began working with DeRoyal Industries to devise an RFID-based solution that would help the hospital better deal with all of these issues. DeRoyal started providing operating room management software 35 years ago. In 2002, however, it sold the OR software portion of its business to General Electric (GE). Since then, DeRoyal has continued its interest in OR efficiency solutions, according to Brian DeBusk, the company's CEO. The firm began meeting with UT Medical to determine whether an RFID system would help it to manage its tools and supplies. UT Medical is currently using OR management software provided by GE.
After conducting some research, DeBusk recalls, the hospital found that the solution was surprisingly simple. Beth Kaylor, DeRoyal's director of clinical innovations and a former OR nurse, recommended installing an RFID reader and antenna in a trashcan to read discarded supply packaging.
UT Medical opted to start piloting the system within its five orthopedic operating rooms because they were used by a smaller group of surgeons. DeRoyal and UT Medical began lab testing before installing the system in a trash bin within each room. An Impinj Speedway Revolution reader is installed outside each bin, with a Laird antenna running inside it. A screen mounted on top of the bin displays the collected read data, which is also forwarded to DeRoyal's cloud-based software.
The hospital's surgical supply distributor, Seneca, RFID-tags most of the supplies it sends to the facility, regardless of cost, including sutures, gauze and other materials. The company uses passive EPC ultrahigh-frequency (UHF) RFID tags from a variety of vendors; DeRoyal and UT Medical are still considering various make and model options for tags used in the future. Any supplies that are not tagged by Seneca, Ashin says, are being tagged onsite at the hospital, using a Zebra Technologies RFID printer-encoder.
Data regarding each item is already stored in the GE software. That information is forwarded to the Continuum OR software as RFID tags are first interrogated, thereby creating a link between each tag ID number and the corresponding item itself.
Staff members are still using the doctor preference card to pick the items required for each surgery, load them on trays and deliver those trays to the OR. Workers enter a patient's ID number into the DeRoyal software when each surgery takes place. DeRoyal uses data about the procedure, such as the type of surgery and the doctor performing the operation, from the GE software. Then, as discarded wrappers are thrown in the trash, the UHF reader captures each wrapper's unique ID and populates a list of products used for that surgery.
In the future, that list of used products will be shared with the GE software for billing purposes. However, Ashin says, such integration has not yet taken place, so the system currently only stores that information for the staff use in determining which products were used, and when.
The five-OR pilot has continued for the past six months. One of the most important findings from the pilot, Ashin reports, is that there is no item too low-cost to be tagged. While most hospitals are employing RFID to track only the high-priced goods at their facility, UT Medical sees value in tagging everything from gauze to implants. That, she says, is because the system can identify a safety concern before a problem occurs. For instance, if any supply is due to expire, or should not be used on a specific patient based on the type of surgery being performed, the DeRoyal software displays an alert on the screen above the trash bin, warning the staff not to use that product.
Typically, when an item's tagged packaging is discarded, the product itself has not yet touched the patient. "In the future," Ashin states, "we plan to scan [read] all items picked and returned for a case [surgical procedure], to catch this before the item is opened."
DeBusk says DeRoyal opted against using high-frequency (HF) RFID tags because they required that personnel place each tag within close proximity of a reader, which would disrupt their activity. Because each trash bin is shielded to prevent stray reads from outside the bin, the antenna can capture every tag's ID number as that wrapper is discarded, without requiring workers to change their own behavior by remembering to scan each item as it is used. "The only thing they do differently is use a different trash can," he notes.
During the past six months, Ashin says, the Continuum OR system has provided employees with the data they need to better identify which items should be delivered for each surgery, by showing which ones had been actually used during similar procedures in the past, though the company has still used the doctor preference cards and will continue to do so. Using data from the RFID system enables the staff to start leaving off items that are never used for specific procedures, thereby reducing the number of times that an asset is taken out of storage and returned.
"It gives us a better handle on what needs to be in each room," says Heidi Auer, a UT Medical orthopedic operating room nurse. As the solution is being deployed to the hospital's other surgical rooms, the facility is also investigating how an Impinj xArray reader installed on the ceiling might be used to gain real-time data indicating what is in each room, thus making it easier for personnel to find something that is required for a particular procedure but is not necessarily on the surgical tray in that OR. That data could also be used for stocking purposes, Kaylor says.
In addition, workers could utilize a handheld reader in stock rooms or in a surgical room without an xArray reader to conduct an inventory count of items that are in stock, and to find any products due to expire. The handheld could also be used to locate any goods that might have been recalled. Additionally, the DeRoyal software will enable the medical center to quickly identify any patient who might have received treatment with a recalled product.