May 19, 2015The East Ohio division of energy company Dominion is employing passive high-frequency (HF) 13.56 MHz RFID tags to reduce the risk of error, as well as the amount of labor time that workers spend collecting and storing data regarding aboveground pipeline inspections. The system includes IDBlue readers paired with smartphones or tablets via a Bluetooth connection, and software from Field ID. With the technology, inspectors can access data about the corrosion inspection and remediation history of each section of aboveground pipe and related equipment, as well as update that information while in the field.
Gina Rundo, a technical specialist at Dominion East Ohio, described how the company has benefited from its RFID technology installation at the RFID Journal LIVE! conference and exhibition, held last month in San Diego, Calif.
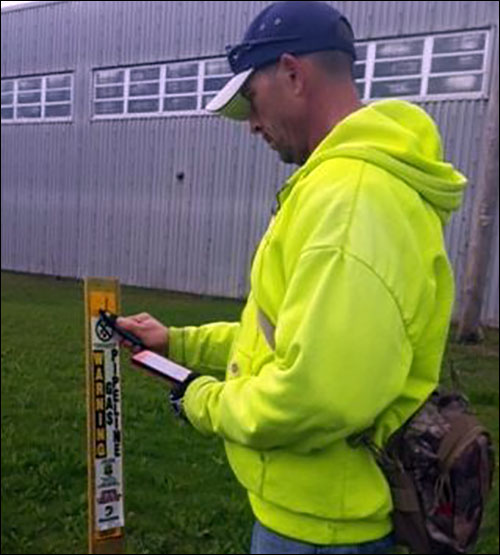
Dominion East Ohio delivers natural gas to 1.3 million customers. One of the company's responsibilities is to ensure that all aboveground pipelines are properly maintained. According to state and federal regulations, the firm must inspect all pipelines exposed to the atmosphere at least once every three years.
Until the RFID system was installed, Dominion East Ohio managed the pipe inspections and maintenance activities via a manual process. When staff members went into the field to inspect a station—encompassing numerous pipelines—they used paper and pen to manually indicate which station was being inspected, and whether that station passed inspection or required follow-up remediation, such as cleaning or repainting. While in the field, the workers lacked access to the inspection or remediation history of each station being inspected, and were thus unable to determine what previous remediation (such as a recoating of paint) might have been carried out to keep it in good condition, or view photographs showing what the pipe had looked like during a prior inspection.
Once finished with their work, inspectors delivered their paperwork to an office clerk, who input the information into the in-house software. The process was not only time-consuming, but also left room for human error, since workers in the field or office could make mistakes while recording information, such as pipeline ID numbers. In addition, there was no way to ensure that inspectors actually stopped at each area throughout a station to inspect every pipe component, versus simply writing up a report claiming they had done so.
In October 2014, the company began deploying an RFID system using passive HF RFID tags to ensure that inspectors had to be onsite and directly in front of the pipeline in order to fill out details about an inspection. The RFID solution would also automate the written data-collection process.
Dominion opted for a custom-made InfoChip tag that could withstand extreme cold and humid weather, as well as rain, snow and ice. "We're in Northeastern Ohio, so we needed a rugged tag," Rundo said. The company initially piloted using a laminated RFID tag, as well as a laminated "notice" tag attached to the pipeline along with the RFID tag, but the notice tag lasted no more than four months before becoming damaged, she explained. InfoChip's customized tag, measuring 2 inches by 3 inches, is encased in stainless steel and epoxy, and contains printed text about the specific pipeline for employees to read visually. The tag is attached to the pipe via a weather-resistant zip tie. The unique ID number encoded to the RFID tag is linked to data providing a description of that inspection zone, including pipe information, location details and a photograph of the zone, which are all displayed in a smartphone app provided by Field ID.
Inspectors use the Field ID app on an Apple iPhone that they carry with them while conducting their inspections. The iPhone is paired with the HF reader via Bluetooth. First, an inspector uses the reader to capture the tag's ID number and transmit that data to the phone, where the app links that ID to that inspection area. The worker then follows prompts on the app to complete the inspection, by providing condition ratings with corresponding photographs, and uses the phone to photograph that length of pipe. The data is auto-populated into a custom PDF file that could then be reported on, exported, or sent to internal or external colleagues.
The system, which was taken live last year, has made the process easier for employees and has helped to prevent errors, Rundo reported, since the data is being collected directly from the source. She added that it also helps prove that an inspector was directly onsite at the time, rather than merely filling out forms as if he or she were there.
Another key benefit to the RFID system is onsite audit verification, Rundo said. "When an audit is performed at one of our stations," she explained, "we no longer have to go back to the office and retrieve records justifying we are compliant. We can now do all of this onsite during the audit by scanning the tags and displaying activity dates, as well as before and after photographs."
In addition, Rundo noted, this process has improved productivity in many ways. One example is the elimination of the need to conduct station tours for remediation bids. "Now that the inspection data is auto-populated to a PDF," she stated, "we can then send the work-order information directly to the contractors who are bidding."
In this case, the PDF provides all information that the contractor requires to bid, including a photograph of the entire station, an individual photo of the station's subset inspection area, inspection ratings and individual photographs. It also includes square footages of piping and equipment (for use in determining the cost of paint and materials), remarks regarding the station's surroundings (such as residential or rural information), GPS location, inspector names, dates and timestamps. "Historically, this would be a very time-consuming process to conduct station tours," Rundo explained, "and truly not efficient when you have a large scope of work and require getting started as soon as possible."
The solution also allows Dominion East Ohio's managers to view all data collected in real time, thereby enabling them to know an inspector's current status at any given time, such as driving to the site or experiencing an inspection delay.
In addition, Dominion created a feature that allows managers to view each inspection area on a map within the company's software. Every inspection area is represented by a color-coded pin to reflect status. For example, a green pin indicates that a station's inspection status is good, a yellow pin represents a station area that is within 60 days of approaching a scheduled inspection or remediation, and a red pin indicates that the station area's inspection is overdue.
Any pin with the letter A on it indicates that a follow-up remediation or action was assigned to a worker. "This provides us with a unique way to track compliance and manage working crews by geographical areas and coded pins to reduce mobilization and time costs," Rundo said.
The next phase of the deployment, according to Rundo, will consist of tagging utility markers that also must be maintained on a regular basis. In this case, Dominion field workers will use the tags to update inspection data related to each marker. The company has been piloting the system on the markers, she said, and hopes to take it live by the end of this year.