Dec 03, 2012VA Ann Arbor Healthcare System is employing WaveMark's RFID-enabled cabinets to track equipment used on patients at its cardiac catheterization and electrophysiology laboratories. The WaveMark solution provides the Michigan veterans hospital with real-time data regarding the use of goods stored on its shelves, as well as their status, such as pending expiration dates. That information is then shared across Veterans Integrated Service Networks (VISN) 11 hospitals, using Intelligent InSites' integrated software platform, as part of the VISN 11 contract with Hewlett-Packard Enterprise Services (see Veterans Affairs Implementing RTLS Across Seven Midwest Hospitals and How RFID Is Transforming VA Hospital Operations).
VA Ann Arbor Healthcare System is the first of several hospitals to utilize WaveMark technology within VISN 11. The John D. Dingell VA Medical Center, located in Detroit, has also installed the system this year, while the Richard L. Roudebush VA Medical Center, in Indianapolis, is currently in the process of deploying the smart cabinets within its own lab.
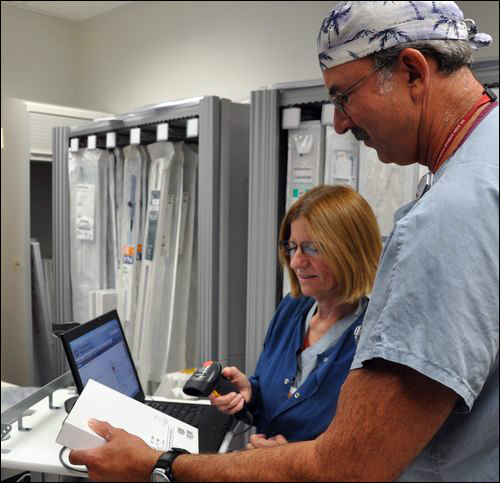
WaveMark's smart cabinets have built-in 13.56 MHz RFID readers; the company employs readers complying with the ISO 15693 standard, with reader antennas installed on each shelf within the cabinet, in order to identify tagged stents, catheters and other medical goods stored inside, as well as standalone encoding or reading stations. In addition, WaveMark provides the software that manages the data, and displays that information for users through Intelligent InSites' real-time location system (RTLS) software platform on a VA-hosted server. By using this technology, says Angie Hernandez, the hospital's logistics and supply manager, VA Ann Arbor Healthcare System has been able to attain visibility into the location of its equipment for use at its two labs, as well as reduce the risk of products expiring prior to use.
The solution was installed over the course of a single weekend in February 2012. All items valued at $50 or more were tagged with a passive high-frequency (HF) 13.56 MHz tag. WaveMark installed a total of 13 smart cabinets and two extended point of service (XPOS) stations for identifying goods as they are used in patient procedures, says Carola Endicott, WaveMark's senior VP of operations, who notes that WaveMark's solution uses a variety of RFID tags and readers to accommodate different product sizes and storage needs. The cabinets and XPOS stations transmit data to WaveMark's software on the hosted server via an Ethernet connection. Each XPOS station consists of a touchscreen computer, an RFID reader and a bar-code scanner.
With WaveMark's cabinets, the RFID readers automatically provide an electronic record of what is in stock every 30 minutes. When a new product arrives at one of the labs, a worker attaches a passive HF RFID tag to that item and utilizes a WaveMark registration station to scan the product's bar-coded universal product number (UPN), lot number and expiration date, as well as store that data, along with the RFID tag's unique ID number, on WaveMark's server. The tagged item is then placed on a shelf within a WaveMark cabinet. Some manufacturers are tagging their own products and registering those tags in WaveMark's system before shipping the products to the hospital. In those instances, hospital staff merely place the tagged items in the RFID-enabled cabinets.
Both labs are adjacent to a control room, where clinical staff members, such as cardiovascular technologists and nurses, can observe the procedure from behind a glass window, monitoring the patient's vital signs and other details. Behind that window is also an XPOS station, with the reader's antenna facing the lab.
To start a procedure's electronic record, control room employees use the XPOS station's bar-code scanner to enter the patient's ID number, then use the touchscreen to select the physician and staff members, and press start. Personnel working with the patient in the lab then wave each stent, balloon, guide wire or other item next to the window as it is being consumed, thereby allowing the XPOS unit to read the item's tag ID through the glass, and creating a record of which items were consumed and on which patient they were used. That data is then forwarded via an interface from WaveMark to the hospital's GE Healthcare hemodynamic recording system software. Once the procedure is complete, a member of the control room staff presses a stop button on the touchscreen, and the software's timer functionality creates a record indicating how long the procedure lasted.
"We have probably recovered items that would have been lost otherwise," Lewandowski reports, since workers can now see not only what was missing but where its tag was last read. This enables the staff to conduct a search to determine if the item was misplaced, fell behind a shelf or was used on a patient without its tag being waved in front of the reader at the time of the procedure.
The hospital currently has approximately 2,100 tagged items stored within the smart cabinets, though the quantity changes regularly as items are removed or returned, and Hernandez can view those changes in the WaveMark system. This, she says, spares the staff hours of time previously spent entering unoccupied labs and updating inventory. A list in the WaveMark software also indicates which items have reached, or are nearing, their expiration dates, as well as in which cabinets those items are located. That same data can be provided in the event of a product recall, thereby allowing employees to identify where the recalled items are located and retrieve them.
According to Hernandez, the technology has "created a revolution" for material management in the labs. "It's making my life more interesting," she states, "because I have so much more information." For example, she says, she can now track which products are being used, when this occurs and by which doctors, and can then approach those individuals to determine whether some products have become more popular, or whether they may no longer need to be stocked.
For instance, the radiology department uses some of the same stents as those utilized within the cardio lab. If a situation arises in which one department needs such stents right away, it can access the system, determine that there are more in stock at another location and use those stents, instead of spending a lot of money on an emergency shipment from the vendor, or canceling the patient's procedure. If one hospital uses a product much more often than another, inventory managers will be able to observe this fact and either transfer or cross-level stock, which would be more efficient and save the VA more money, explains Colin Betts, VA Ann Arbor Healthcare System's supervisory inventory-management specialist chief.
"Usage is also tracked more efficiently," Betts says. "It is easier to see if a product doesn't move or turn very fast, so less of that product can be stocked, leaving room for more fast-moving items. This is especially important, because space is at a premium. The hospital is increasing its caseload, and hence its procedure areas, but without increasing its footprint."
The hospital intends to open a third laboratory during the coming year, which will also use the WaveMark system. This will include additional cabinets and a third XPOS station.